Building smarter
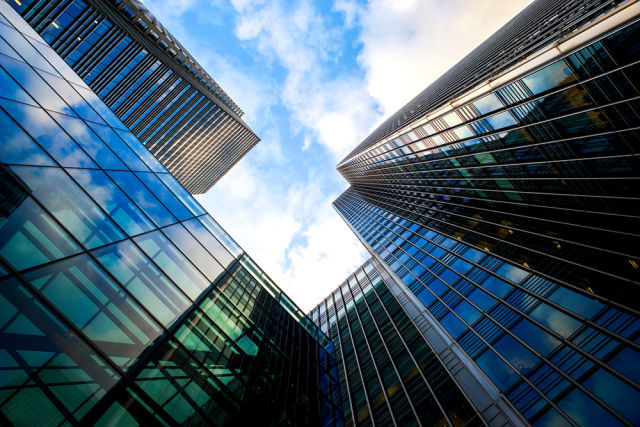
Construction and information management specialist Stuart Bell shares his views on the industry’s use of the latest tools such as digital twins.
The construction industry is in a new digital decade. With the 2010s paving the foundations for the sector’s digital frontier, digital construction is enabling people and key stakeholders to create better-performing estates with scalable, mappable futures.
As with the dawn of any new age, the promise of uber-modern technologies on the horizon will be hugely tempting. Cloud collaboration, robotics, augmented reality; these unique innovations might be in the hands of every member of the supply chain within the next 20 to 30 years.
Before we indulge ourselves too much, the industry has to remember that it has been notoriously slow to adopt technologies, typically but not exclusively as a result of the great culture change and investment required to digitally transform the business at hand. Even if businesses have implemented technologies, such as the likes of a common data environment for instance, the scale and format in which these systems have been implemented differ from one business to another.
Digital maturity and adoption also hinges on whether a business has a vision of what they want the technology to achieve. Which data needs mapping? What are the current work processes? What is their BIM strategy? All of these questions feed into a business case for adoption. Often, however, these questions are not communicated when they should have been, leading to an unfortunate level of ambiguity as to why technology was ever considered in the first place.
It feels as if digital construction is far from a utopia, but near enough to be a reality. Many businesses across the sector see some technologies as simply not worth their time and effort, even though the benefits are colossal. It is, then, crucial to demystify and thus educate people on the differences that can be made, beginning with the one which has a positive impact on people and process: digital twins.
Although the industry has been hesitant to adopt new technologies and ways to work, it can unanimously agree that digital twins are having a beneficial effect across the supply chain; helping to store and manage data, use data to enhance the build and future operation of an asset, and prevent risks.
Since the mid-90s, the industry has been trying to improve how its workforce manages information. Email took over from paper and this extended to the internet, which provides a common interface where information can be accessed. The subsequent proliferation of broadband and mobile has meant the industry has been able to capitalise on technology and make it business as usual.
But for some within the supply chain, the concept of a digital twin is still hazy. Whilst key stakeholders and the majority of Tier 1 organisations are fluent in the benefits of digital twins, others are unfortunately lagging behind; unsure of how favourable digital twins are and whose responsibility it is to manage them.
In essence, a digital twin is a virtual representation of a physical asset, which provides up-to-date data on the real world operation of a built asset. A digital twin houses information on a given asset, such as its objects and states. Digital twins cover the entire lifecycle of a building, connecting products and services so they can be viewed and, if necessary, acted upon during construction and after handover to the asset owner.
When it comes to unravelling a digital twin’s definition, industry professionals up and down the supply chain must see the digital twin as more than a file containing everything which relates to an asset. Yes it houses data, but it also assures the information is spatially-connected and held altogether in the right place, to maximise productivity and product performance.
A digital twin is, therefore, all about connection. It would merely be a virtual representation of a building with no real-time value if the data within were not connected to the physical asset.
Think of a digital twin as a ‘top hat’ which connects different systems and sensors together, through a virtual representation of an asset. A digital twin isn’t something which sits in isolation. Using sensors, it is bound to the physical asset to give a true to life, equal image of the built asset.
Furthermore, digital twins, BIM and smart buildings are interlinked. BIM provides the static data and information for the design and construction of the asset, and digital twins enable a fluid representation of the asset across the lifecycle. Smart buildings use the Internet of Things (IoT) to track and optimise performance. Digital twins then simulate complex scenarios to mitigate risk, which is hugely desirable for FM and operations departments preserving the integrity of an asset.
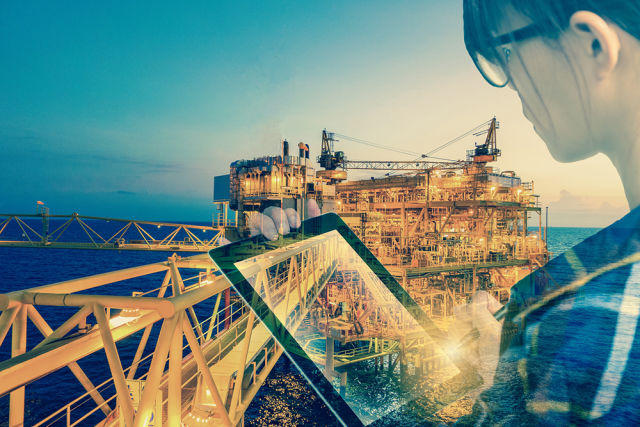
The responsibility of who owns the digital twin when it is handed over to the asset owner is a complex factor, which puts to debate questions on ownership, security and accountability.
Some may argue that administering responsibility to all parties is a recipe for digital chaos. The ‘manager’ should be whoever the asset owner contractually states. That way, the asset owner can be very specific about how information and data are presented and stored, and who is responsible for updating information models.
On the contrary, others in the industry believe the digital twin is everyone’s responsibility: the operations and FM teams, company administrators plus key stakeholders. As the digital twin is able to access and store live sensor data, the supply chain will have to procure information differently and make better decisions to assure the efficient performance of the physical asset. For that reason, it is arguably healthier for everyone to be speaking the same language from the start.
A digital twin is essential vessel which unites the supply chain through standards and processes and encourages a collaborative working environment that will enable the interconnection of all these datasets.
In summary, a digital twin provides multiple views on connected data, utilising the physical location of an asset as the primary navigation route, to reflect real-time performance, enable cost savings and drive efficiencies across the supply chain.
Digital twins might just be the technology that will make a difference to the construction industry. The connectivity capability of the new generation of systems will unlock all the value currently stored away in siloed systems, to become available through a single, user-friendly interface with a 360-degree, real-time view on the operation of a built asset.
Stuart Bell is project and asset information management provider of GroupBC
Picture credits:
Looking up to buildings: iStock/alice-photo
Woman with clipboard: iStock/Theerapong28