The pressure’s on for legacy heating systems
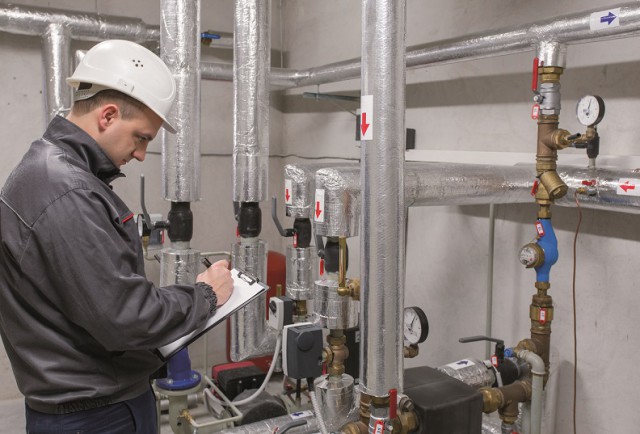
Resolving issues with legacy heating systems is often not straightforward.
It’s fair to say that as technology has advanced so commercial heating systems have improved. Today they are more effective and more reliable, delivering better results and greater energy efficiency.
However, there are uncounted numbers of legacy systems in offices, factories, school and other large establishments where time is catching up with them.
Performance levels have dropped and the normal maintenance regime is no longer enough to put right what’s gone wrong and to meet ever rising expectations around service and efficiency.
To bring them back to acceptable levels of operation, and meet modern standards, it’s time for a refurbishment.
Experience shows no two failing systems are the same, although the complaints can be common: cold spots in radiators, noisy pumps and pipework, high energy consumption and poor output.
Those are the effects, and sometimes the solution can be relatively simple, such as the installation of deaerators and dirt separators to solve the issue of harmful air in the system, which left unaddressed will lead to corrosion.
But often a detailed inspection will show up more complex problems, and expose the fact that earlier efforts to sort these have been more of a fudge than a fix.
Rather than replace failing or outmoded components, which might involve short-term costs but be cost-effective in the long run, attempts have been made to tweak the existing inadequate set up, only for it to fail again resulting in continued poor performance and another call-out to the engineer.
Negative pressure
One recurring issue, particularly with larger buildings such as tower blocks and high rise offices, is negative pressure at the top of the system.
If the pressure is too low comparative to the height of the building, water will not fill it, resulting in large quantities of air in the pipework.
This has led to workers and residents on the upper floors of tall buildings being left without sufficient heat or hot water. But simply boosting the pressure does not necessarily solve the problem, it can be far more complex.
In one example, the system was regularly manually vented but within a few weeks the problem was back. Just adding automatic deaeration equipment to remove the air, without taking other measures, would simply have exacerbated the situation.
The negative pressure would have sucked more air in through the automatic vents at the top, and the fresh influx of oxygen would have accelerated corrosion in the system, with the potential failure of ferrous elements.
The core of the problem was that the baseline pressure regime was wrong and there would be no point in adding any deaeration equipment until this had been addressed.
Contributing to the issue was that the expansion vessels were undersized and on the return side rather than the flow side of the circulating pumps.
This meant the system fluid was being pushed into the heat exchanger rather than being pulled through. A key element of the overall solution was to relocate the pumps on the flow pipework, which would increase both the pressure and fluid volume, improving the flow characteristics to all floors.
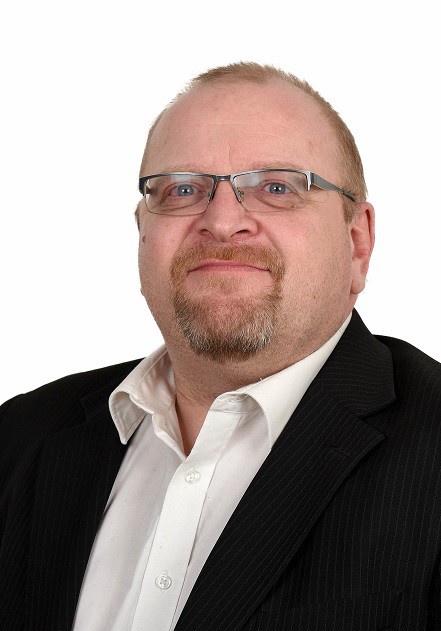
To complete the refurbishment, larger expansion vessels were proposed, correctly pre-charged, with a vacuum degasser unit installed to remove the air in the system fluid, the vacuum degasser being powerful enough to remove all the free air, microbubbles and dissolved gases.
Vessels and valves
Undersized expansion vessels are a common occurrence. In some cases it may be been necessary to replace undersized vessels with multiple larger, correctly sized vessels.
The two British Standards that provide the relevant guidance for central heating systems are BS EN 12828 and BS 7074.
BS EN 12828 covers the design of water-based heating systems in buildings, while BS 7074 gives guidance on the correct specification for expansion vessels.
To arrive at the correct pressure range for the expansion vessel in relation to the size and demands of the building, the designer has to adhere to both. But with some installations the full calculation hasn’t been done, resulting in the vessel being undersized for the system.
While the pressure might be too low for the system, it is too high for the vessel, leading to the safety valve lifting.
This can lead to water loss, chemical pollution, and potentially a multitude of problems simply for not doing the full calculation.
Sometimes, to avoid water loss, safety valves have simply been replaced with higher rated ones. But this is an inadequate fix if the overall pressure regime is not addressed.
It is worth nothing that to meet the relevant British Standard, the system’s high pressure setting should not exceed 90% of the rating on the expansion vessel’s safety valve, with the differential at least 0.5 bar. This is to allow for manufacturing tolerances in the springs that operate the safety valve.
Long-term solution
Taken in isolation, it could be that each individual component in a system is in accord with the requirements of the original specification. However, the way the system has been configured is causing issues.
There is a fundamental problem with the design that needs to be addressed, and just tweaking what is installed will not provide an effective solution.
Taking comprehensive action now will be a better investment long-term, with repetitive problems eliminated, component life extended, and the system operating more efficiently, with the additional benefit of reduced maintenance and call outs.
Steve Simmonds is Special Projects Engineer with Spirotech