Rubber bellows life cycle & specification

Eddy Warren of Supaflex Agencies stresses the importance of how to prevent sudden burst failures.
A large number of clients have suffered very seriously in recent years with sudden burst failures of rubber bellows on their pumps and plant, especially on LPHW and MPHW. On CHW, CCW and MWS Booster sets etc, where working temperatures of the systems are much lower this is much less so, but with poor FM and maintenance it still sometimes happens.
A flooded plant room with water at elevated temperatures from LPHW, MPHW, Primary HWS and Secondary HWS, particularly in a hospital where the HWS is kept to 65 Degrees C to avoid Legionella, can be a huge problem. Not only enormous costly damage to the plant and equipment but the building and equipment in it too.
Some M&E Consultants specify rubber bellows by using the German DIN 4809 Specification. This is due to the fact the UK do not have a BS EN Specification equivalent. This is not an ideal position and is being evaluated. There have been one or two cases of high temperature burst failures of low-grade rubber bellows failing and causing injury. Waiting until a fatality occurs should not be an option!
Fixborough Disaster
Many reading this will be too young to remember the ‘Flixborough Disaster’. On the 1st June, 1974 at the Nypro-Cyclohexame production plant in North Lincolnshire, 28 were killed and 36 injured. Had it been a weekday, with many more staff on site, many more fatalities and injuries would have occurred.
The rupturing of a 500 mm (20”) Stainless Steel Metallic Bellow at the connection balance pipe bypass, between 3 vessel/reactors, containing the Cyclohexane was the cause. A crack was found within the middle vessel and was removed. The support of the balance pipe bypass was poorly supported and its gradual collapse was not noted until after the huge explosion and fire.
Worldwide standard
It wasn’t until 1981 that the first BS Spec. IE BS 6129-1, covering metallic bellows, came out. The worldwide standard for Metallic Bellows is covered by EJMA (Expansion Joint Manufacturers Association) whose headquarters based in the USA, are recognised by major manufacturers across the globe.
Rubber bellows used in building services engineering are mostly EPDM with steel collar reinforcing and nylon reinforcing within the body. The degradation of the nylon at high temperatures is substantial. High-grade rubber bellows are not reinforced with Nylon in the body.
In the mid 70’s full steel cord mesh was used but this was found to fret through the EPDM wall. The discovery of Kevlar (Aramid Fibre) meant it could be used for many years. In recent times this has been superseded by the use of Polyester Ether Keytone (PEEK).
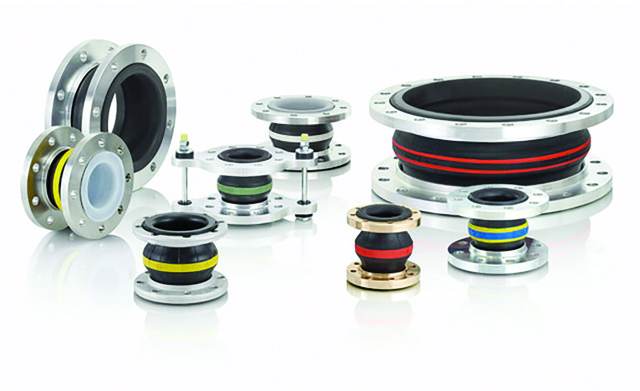
Only a very small number of rubber bellows manufactures are approved under DIN 4809. All are European and there are one or two American manufacturers who could be. Those who are not should never be used on LPHW or MPHW and preferably not with lower temperature services either.
It is also very positive to see many specifications written for Middle East Projects not permitting low grade rubber bellows use. They are often banned by their own governments.
Clients can fall victim
All M&E Consultants need to carefully evaluate their specification page on this. An unclear specification results in a contractor finding a very cheap low-grade rubber bellow. Unsuspecting clients can fall victim to huge costs after in only a few years. Predominantly when their FM and Maintenance teams have to correct the problem. Installing high-grade units in the first place can prevent and help safeguard against bursts and potential injury.
RBMA
The formation of the Rubber Bellows Manufacturers Association (RBMA) has been instigated to only allow membership from Manufacturers of High-Grade Rubber Bellows. Manufacturers and Suppliers of low-grade rubber bellows only are not permitted to join.
A BS EN Standard is long overdue to eliminate the use of low-grade poor-quality products being used. In the short-term, high-grade can be more costly. However, in the long term the use of these units can be more cost effective and much safer.
www.supaflex-agencies.com