Planning for winter
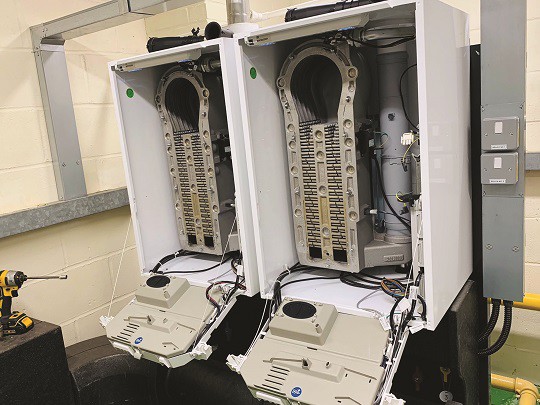
Baxi Heating’s Technical Director Andy Green discusses the importance of implementing a robust winter maintenance programme to protect a building’s heating system and ensure its smooth running
In a year like no other, the role of HVAC services in ensuring that buildings are functional, efficient and safe has come firmly under the spotlight. Air quality and ventilation systems have undergone increased scrutiny to mitigate the risk of COVID transmission in buildings. But as we head into the coldest months of the year, when demand for heat is at its peak, it’s vital not to forget the building’s heating system.
In the current economic climate, businesses and organisations might be tempted to disregard regular maintenance. But to neglect it is a false economy. If heating equipment is inadequately maintained, it may well be working inefficiently and adding an unnecessary financial burden to already tight budgets. To put it into perspective, in our experience, a boiler or water heater that isn’t properly maintained can cause heating costs to increase by as much as 30%.
Ensuring that a full check is carried out at regular intervals will enable any potential problems to be identified and early preventative action taken. This can avoid the need for more expensive repairs or, worst-case scenario, an emergency replacement that could require the closure of the building and/or potentially costly extended downtime.
Take boilers, which are at the heart of the heating system in many commercial buildings. To continue to operate reliably and effectively throughout their life, they need looking after with a regular service that will optimise their efficiency and thermal comfort within the building.
A typical service will include cleaning of both the heat exchanger and condensate trap, flue-gas analysis, checks on gas pressures and interfacing connections like the flue, controls functionality, and water treatment.
The service should be carried out as per manufacturer instructions and using only genuine parts to optimise asset performance and longevity while ensuring full compliance with an existing warranty. To save on time and costs, look for manufacturer service kits that contain all the genuine parts required for a first-time fix. This has the added benefit of minimising disruption for end users.
Water quality
Water quality should also be tested at regular intervals. Heating and hot water systems perform better, more safely and more reliably with good quality water circulating in them. Routine monitoring will highlight any issues early on, helping to save money in the long run.
Without the appropriate treatment, scale build-up, settled sludge and microbiological contamination in a closed-circuit system can lead to inefficiencies, poor performance and potential equipment failure after even a relatively short period of time.
BSRIA, ICOM and leading heating manufacturers all recommend implementing into the maintenance regime routine flushing, chemical cleaning and the use of appropriate inhibitors to minimise the corrosion of system materials, prevent the formation of mineral scale and prevent growth of microbiological organisms.
In buildings that have been closed for a short period of time, it is critical, when reactivating them, to implement a full water treatment and legionella prevention programme that will include pasteurisation, microbiological sampling and chlorination of domestic hot water systems where required. For further advice on the control of legionella bacteria in water systems in operational buildings, the HSE Approved Code of Practice HSG274 offers practical guidance.
Controls
Control settings for both the boiler and the Building Management System should be checked on a regular basis, with settings adjusted to reflect building occupancy and usage to optimise energy efficiency.
If a short-term building closure is anticipated, either over the Christmas holiday or due to local COVID-related restrictions, we recommend leaving the system in operation but lowering the outputs. This will avoid the possibility of damp entering the building, reduce the risk of microbial contamination which can cause corrosion, and help building operators keep energy bills down.
Ensuring that the controls are set to offer the building frost protection and background heat will also help to avoid the possibility of the pipes freezing in the cold winter months.
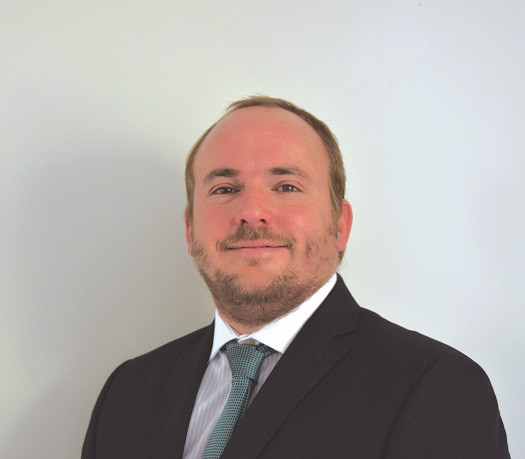
Planned replacement
Even well-maintained boilers will eventually come to the end of their serviceable life. So it’s advisable to start assessing the efficiency of the existing equipment, identifying funding opportunities and planning replacement programmes.
In today’s uncertain and straitened times, taking a proactive approach enables organisations to budget ahead, thereby avoiding unanticipated expense, and plan staged replacements to minimise disruption.
When selecting new boilers, efficiency, reliability and ease of installation will likely be key priorities. But ease of future maintenance, servicing and part replacement should also be evaluated to help maintain high performance throughout the product’s lifecycle. Checking that manufacturer spare parts are readily available will also make it simpler to keep the heating system operating as intended in the future.
Evolving technology and techniques
Forward planning provides time to research new heating technologies and techniques. Manufacturers are continuously evolving their products and innovating to meet modern heating demands. New enhanced features including improved boiler control, connectivity and flexibility will not only make life easier for consultant engineers and contractors at the design and installation stage but simplify maintenance and operation, lowering the total cost of ownership for the building owner.
While physical distancing requirements are still in place, using turnkey prefabricated and preassembled boiler rig modules should also be an option. With fewer workers – and fewer skills – required on site and for less time, offsite fabricated options like these can reduce installation and commissioning time down from weeks to just days while providing assurance that the exact specification is met.
There is additionally the option to future proof the rig so that another boiler can be added at a later date. This is beneficial in buildings that are planning phased boiler replacements or anticipating an extension to the building.
Consider too selecting boilers with a high temperature differential and wide operating range as by providing the perfect heat source for low carbon hybrid installations, they will again help future proof the system.
Agile response
Now more than ever it makes perfect financial and environmental sense for businesses to actively avoid unnecessarily high bills and needless energy waste. And if heating is the natural starting point, then implementing a robust maintenance programme is the next logical step.
Heating engineers, facilities managers and building operators have a key role to play in this. With a comprehensive, planned maintenance programme in place, businesses will be able to rely on a reliable, energy efficient heating and hot water supply this winter, even in an extreme cold snap.
And while there is now hope on the horizon for a full recovery in Spring, a flexible approach to opening and closing buildings will likely be essential in the next few months to enable companies to bounce back rapidly. A robust maintenance schedule will be beneficial in helping them adapt rapidly the way they operate heating systems to best meet the differing occupancy rates and building usage.
We in turn look forward to supporting the building services industry with our quality heating solutions, value-added services and strong technical support that make for simpler maintenance and optimum performance – so that the heating system will be one less concern in these difficult times.
Andy Green is Technical Director at Baxi Heating