The benefits of prefabrication in a COVID-19 world
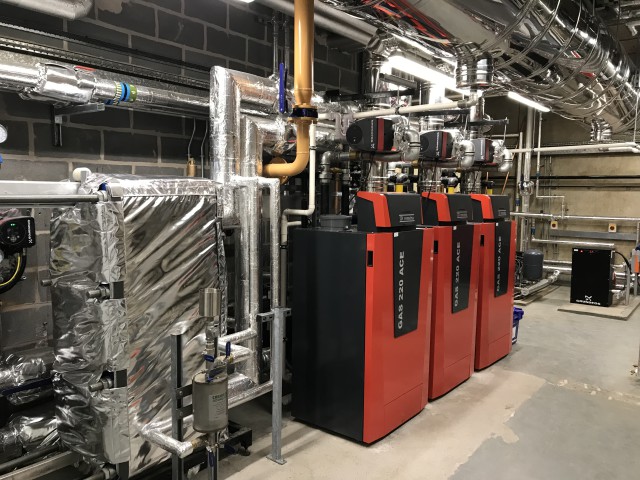
Balancing project delays and backlogs with tighter onsite safety requirements? Prefabricated heating solutions could be the answer
Working in a COVID-19 world has required adaptability and resourcefulness from the heating and building services industries in terms of working practices and techniques.
Take safety. Clearly this should be a priority at all times, but with tighter safety measures in place, the focus has naturally intensified. Added to this is the need to return to delayed projects while keeping current projects on schedule.
How to resolve the challenges? One option that is increasing in popularity is to use offsite prefabricated heating solutions.
Offsite fabrication is well established in the building services industry and increasingly used on heating projects.
A key benefit of manufacturing units or components under quality-controlled factory conditions with end-of-line testing is that it makes the process more efficient and sustainable.
Onsite safety is also improved as fewer workers and skills are required on site – and for less time – reducing the number of hot works and possibility of accidents. Crucially, in current times, this makes it easier to adhere to social distancing and COVID-19 safe working guidance.
It also simplifies logistics – not to mention improving the overall carbon footprint of the project – as it cuts down on the number of workers needing to travel to site. The number of deliveries is similarly reduced, avoiding complicated scheduling issues.
Onsite productivity is boosted as the bespoke design process ensures faster, easier installation and commissioning. And with less potential for delay, it’s easier to keep projects on schedule and make up for any lost time.
Rapid installation
For larger scale projects, there are numerous tailor-made heating and hot water solutions available to meet the needs of every project. These include prefabricated modular solutions, such as packaged plant rooms and energy centres, that are transported to site in modular units for plug-and-play installation, ready for commissioning.
A popular option in multi-occupancy buildings is to fabricate tailor-made modular boiler skids that can be installed in a pre-existing plant room, bolted on to the installed systems or designed to fulfil new build requirements. Similar to plant rooms, but without the walls, they are designed to address the individual requirements for each project.
A Heat Interface Unit (HIU) will typically distribute the heat generated by the centralised plant to the heating and hot water system of the individual apartments. HIU utility cupboards can also be pre-manufactured or pre-assembled, configured to suit the layout, service connections and spatial requirements of each project so that they can be installed in a matter of hours.
Onsite time savings
One example is the recent heating refurbishment project at Valiant House, a 17-storey, 93-apartment, residential tower block managed by housing association Charlton Triangle Homes, part of Peabody Group.
To meet the specification for the centralised plant within the design parameters, our Packaged Plant Solutions subsidiary supplied six Remeha Quinta Ace 115 boilers on a prefabricated skid, complete with pipework, pumps and Plate Heat Exchangers (PHEs).
The existing utility cupboard spaces within each property also needed refurbishing. We supplied a Baxi HIU unit, together with controls and a heat meter, pre-assembled the Megaflo ECO cylinders with the associated pipework, and provided first fix rails for a time-saving solution.
Using prefabrication paid dividends. “The major advantage for us was the time saved on site,” said Ian Winterflood, Head of Electrical and Mechanical Services at Peabody. “The works began at the start of the year, so with COVID-19 restrictions in place just a few months later, we were running a little behind.
“However, thanks to the solution provided, Milverdene, the project contractor, was able to complete the changeover in just one day and then refurbish five properties a day, putting us firmly back on schedule. We also didn’t have to worry about multiple deliveries or materials being left on site as the solutions arrived pre-assembled and ready for installation just when needed.”
Certainty factor
Prefabrication also benefits smaller-scale projects such as boiler replacements. Whether it’s a one-off heating upgrade or a series or plant room refurbishments, using turnkey heating solutions can help meet tight project schedules and minimise system downtime.
Take Remeha’s bespoke boiler rig and cascade systems. These mini plant room systems provide manufacturer design input with pumps, boiler configuration and other components matched to deliver the required performance in an arrangement tailored to the specific site constraints.
The design opportunities are virtually limitless, with options for wall-hung or floor-standing boilers – or even a mix of the two – and low loss headers or PHEs. Ancillary items such as dosing pots and pressurisation units as well as project-specific controls can also be integrated into the design to maximise seasonal efficiency and performance.
Like the larger-scale solutions, they are designed using BIM tools and 3D computer-aided design (CAD) systems, so stakeholders can collaborate on the system design and fully evaluate the functionality before the build begins. In this way, onsite snags are avoided.
Once the design has been agreed and the unit is built, it is delivered to the plant room either as a single wheeled unit or in easily connected modules with insulated pipework set, ready for rapid connection.
The certainty of speedy installation and reduction in number of workers, skills and time required to be spent on site are major benefits at all times, but particularly working in COVID-19 times.
Increased productivity
The time savings from using prefabricated solutions was central to the successful delivery of a major heating refurbishment programme by consultants CJR Midlands and M&E contractor ASBN for Nottinghamshire Police.
Time was the critical challenge as the heating systems at all seven police stations needed to be refurbished in just three months.
CJR Midlands specified a combination of Gas 220 Ace floor-standing boilers with Remeha offsite fabricated cascade arrangements to meet the requirements.
Working with both CJR and ABSN, Remeha prepared 3D drawings of the boiler cascade arrangement to the specified layout for each of the sites and integrated Low Temperature Hot Water (LTHW) and gas headers, pump sets and a PHE into the design.
For ABSN, a major advantage of using offsite fabrication was the ability to prepare the connecting pipework before delivery of the boiler modules.
“Having the detailed, co-ordinated dimensioned designs for each plantroom allowed us both to procure and to preinstall pipework in readiness for the boiler delivery,” said ABSN Director Nick Clews. “This helped speed up the installation process considerably.”
Rise of offsite
Given the considerable advantages of prefab, both on smaller and larger-scale projects, from refurbishment to new build, its rise in use is unsurprising – and particularly so in the COVID-19 scenario.
By encouraging early engagement of stakeholders prior to the build, this approach ensures a quality solution that optimises certainty and safety while delivering the all-important time savings.
The consultant engineer has the necessary design flexibility to meet all project and customer requirements and the assurance that it retains the original specification detail. And it’s easier for contractors to plan ahead and ramp up productivity by putting skills to use on other areas or projects.
With our comprehensive commercial heating portfolio and established prefabrication expertise, we look forward to supporting consultants and contractors with our bespoke offsite heating solutions to deliver prefab benefits both during COVID times and beyond.
Tom Murray is Specification Manager at Baxi Heating