The shape of things to come
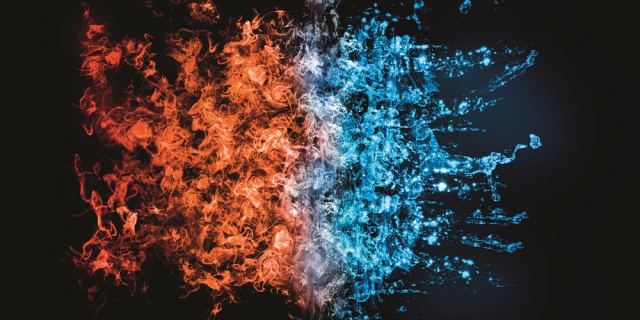
Due to environmental and political pressures, manufacturing and construction companies are starting to replace gas boilers with more efficient products that emit less Co2. The question has to be asked “Will the traditional concept of a white box typically supplied with a first fix rail be replaced by a more practical device to better suit tomorrow’s heating and hot water needs?”
One example of where the gas boiler has been replaced with the white box or a unit of a similar size and shape with the initial first fix rail is the District Heating market.
Group Heating Schemes
District heating is where homes or apartment buildings are not equipped with their own individual decentralised heat generating units (such as a boiler). Instead, they get their heating and hot water needs met by group heating schemes that use a central boiler and shared thermal circuit to supply each apartment’s living space either directly or indirectly through heat exchangers. Depending on the system design there are generally two services served by the two individual heat exchangers, one services the living spaces heating need and the other the living spaces hot water requirement.
To the lay person a Heat Interface Unit (Referred to as a HIU from this point forward) is providing heating and hot water just as a boiler would. And the concept of a large boiler in its own enclosed space within an apartment’s living space is accepted and deemed a necessary in order to provide their heating and hot water needs. Even if in most cases that HIU is taking a significant piece of the apartment’s living space. This acceptance/complacency has allowed HIU manufactures to continue to supply the large space consuming devices that are commonly installed today. Largely only innovating in terms of outer appearance or improved insulation, but until now there has been no real drive to innovate in the direction of making the unit radically more compact.
Dirty water
Additionally, the understanding of the need to gain access to the HIUs for the flushing and commissioning process after installation is critical to the life of the HIU and the life of the entire system. The fact that as most builds commence, access to the HIUs becomes much more difficult and the risks of dirty water finding its way into a finished apartment’s system would not be fully appreciated when deadlines are tight. This can and will often greatly reduce the chance that the HIUs are properly flushed. This becomes even more difficult when the building is occupied and access to the HIU is now controlled by the occupants of an apartment, as dirt that has not found its way out of the system beforehand, now finds its way into the HIUs heat exchangers and the control Valve’s moving parts.
So logically we now arrive at the conclusion that to enable long term peak performance, innovation to facilitate the relocation of HIUs from their traditional space consuming place within an internal service cupboard, to an externally accessible location for easy access by building maintenance is perhaps the best way forward.
Improve performance and lifespan
The simple and obvious solution is to design HIUs that can be installed in a position that allows easy access not just throughout the construction period but also after the apartments are occupied. Furthermore, to improve system performance and lifespan, we should design HIUs to not only comply to the BESA test but also to comply to the BSRIA BG29 2020.

With conventional designs an externally accessible service cupboard could be included in the architectural layout of new buildings or retrofits, that would allow external access to HIUs. But this cupboard would take up a significant amount of valuable space within the apartment’s living space as well as adding a significant cost.
That said, ceiling space, perhaps over a front door opening or at the high-level within a corridor would be largely free and potentially easily accessible externally. However, the current conventional design of HIUs doesn’t lend itself to fitting within the standard 300mm height of ceiling voids, making an external service cupboard the only option.
Therefore, a new Heat Interface Unit has been designed that not only fits into a 300mm ceiling void but also complies with the new BSRIA BG29 2020 recommendation.
A new design concept
This new design takes advantage of the fact that a HIU is not a boiler and can be drastically reduced in size by minimising the internal pipework within the HIU and innovatively configuring the cumbersome expansion vessel. Additionally, with this new HIU design concept, the HIU does not need to be totally encased in insulation but can be strategically insulated to only encompass the vital areas such as inter connecting pipework and the heat exchangers only.
This has the additional benefit of placing all electrical components and connections from the controller outside of the insulation layer. By doing this we reduce their exposure to higher than ambient temperatures which are essential to the HIU’s operation. This in turn has the additional benefit of maximising the overall components life span, which further improves the design’s green credentials (by reducing long term product consumption and landfill).
Martin Lowe is Technical Consultant to Pettinaroli Italy