Making electrical touchpoints safer
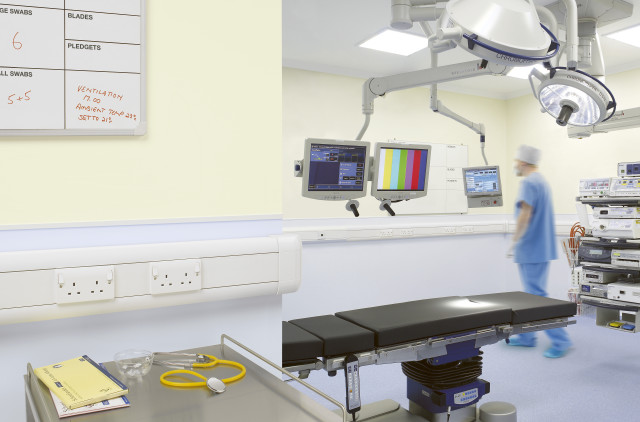
Emma Segelov, MK Electric’s EMEA marketing operations manager, looks at the key areas of concern amongst workers in the UK, and examines improvements which can be made to minimise the spread of contaminants via touchpoints in the workplace.
As we eventually make our way back into indoor spaces, cleanliness and safety will be key factors in reassuring people that a building is safer. Therefore, building owners, operators and employers must reassess not only procedures but also the infrastructure and make the necessary investments to instil confidence amongst staff, customers and other users.
The COVID-19 pandemic has resulted in an increased emphasis on staying safer. This means that as we return to indoor places to work, shop, study and play, many health and safety factors which weren’t top of mind for many people before are now coming under the spotlight. Many stakeholders, including workers, are now keenly attuned to the steps employers are taking to make their premises safer and healthier both now and for the future. What are the perceptions and feelings amongst employees of their workplaces? How can specifiers meet these expectations and that electrical touchpoints can stand up to scrutiny if their hygiene levels are questioned?
Workforce insights
In a recent study commissioned by Honeywell and carried out by Wakefield Research of workers’ perceptions on the health and safety of their workplace, a staggering majority of the workforce in the UK (71%) does not feel completely safe working in their employer’s buildings. This number is even higher for those working remotely (78%), who are especially sceptical about the safety of work sites. In the UK, half of the participants interviewed are equally concerned with transmission of COVID-19 through touching a surface that has the virus (51%) and through the air (49%). In fact, their level of worry for surface transfer is significantly higher compared to other employees around the world (44%).
Although many buildings have made changes to their procedures to address these concerns, investments are not being made to the buildings themselves – and their occupants have noticed. 62% of respondents in the UK believe that their building management is likely to make short-term changes in response to COVID-19 (62%), rather than long-term investments in building systems to keep them safer. With nearly one in five (22%) remote employees saying that they would look for a new job rather than return to a site that did not implement the necessary safety measures, it is clear that workers are going to demand more from buildings in the future. Companies who don’t take the provision of safer and healthier environments seriously enough in the long term, even when the current pandemic ends, could risk losing valuable staff.
Electrical touchpoints
Whether it’s an office, classroom or hospital, buildings are meant to be spaces to bring people together. If they are to continue serving this purpose in the future, building managers and businesses will need to restore confidence in being indoors beyond short-term measures. So, whilst more frequent cleaning, encouraging all building users to regularly wash their hands and social distancing set ups can all improve safety, deploying the right technologies and materials should also form part of the longer-term strategy to create a healthier environment overall.
Electrical wiring devices such as switches and sockets are just one of many touchpoints around a building that can provide opportunities for contagions to spread. Therefore, choosing products that have anti-bacterial and anti-viral properties can help to reduce the risk of infections. Many devices are now manufactured from materials which have these attributes, such as urea formaldehyde, making them an effective weapon in killing harmful bacteria and viruses. Products that are scratch free, thanks to high quality mould tools, such as MK’s urea formaldehyde wiring devices, minimises surfaces for pathogens to hide, providing another way to help stop the spread of infections.
Meeting the standards
To provide additional protection for users against contracting an infection from frequently touched surfaces like electrical sockets and switches, there has been a number of anti-bacterial and anti-viral products introduced onto the market. But not all of them are equal. It is important to take a closer look at claims and fully understand what this means to provide the best levels of protection for building users and make sure the highest standards are being specified.
Firstly, it is worth noting that the test carried out on a product’s anti-viral and anti-bacterial properties should comply with the latest internationally-recognised standard – ISO 22196:2011. This specifies a method of evaluating microbial activity of treated plastics, and other non-porous, surfaces of products. As part of meeting this standard, the product tested must remain in contact with the microbes for 24 hours. The tests also must be carried out under set temperatures and humidity levels. What’s more, multiple test samples are required, and control tests are also done to eliminate variables that are not being examined, maximising the reliability of the test results. Claims made on products that have not been tested to an industry recognised standard such as ISO 22196:2011 may not be as scientifically robust.
Comprehensive testing
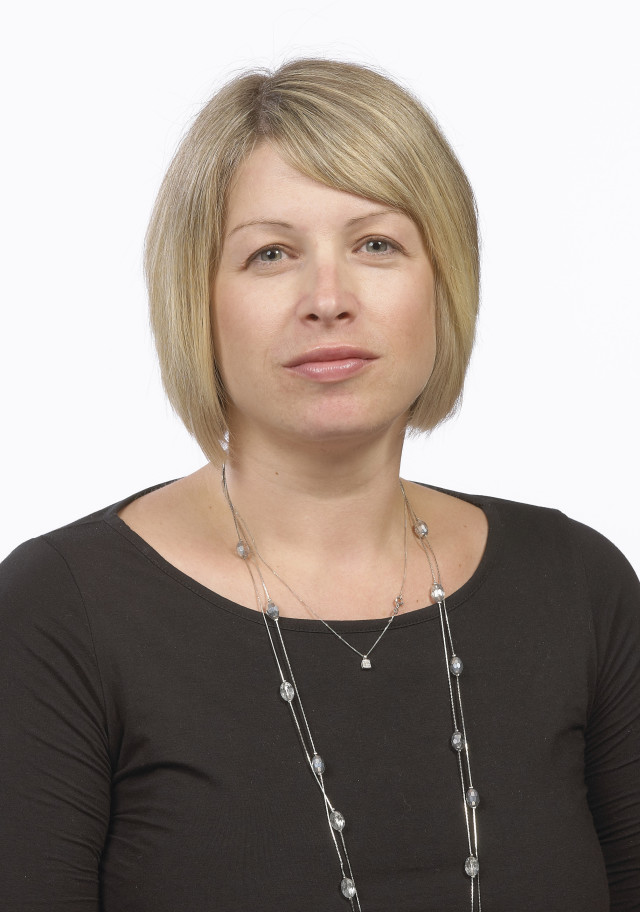
When determining the effectiveness of electrical products in killing bacteria and viruses or preventing their growth, it is also important to look at which types they have been tested against. This means that the products can provide protection against as many prevalent pathogens as possible.
Although the ISO 22196: 2011 test method uses Staphylococcus aureus and E. coli, other pathogens can also be tested without compromising on this standard. Therefore, specifiers should also look for efficacy in fighting diseases caused by other bacteria in a product. Some of these could be more relevant to the end-client’s sector. For example, MRSA lives harmlessly on the skin of around 1 in 30 people,1 but could cause a serious infection if it gets deeper into our bodies. It can do this via a wound, burn, feeding tube, drip into a vein, or urinary catheter, which is why it poses a higher risk to patients in hospitals and other healthcare environments. Our Logic Plus and MK Base portfolios are the most widely tested wiring devices on the market, with outstanding kill rate protection against Listeria, Staphylococcus Aureus 6538p (which is known to be resistant to antibiotics), MRSA, E.coli and Salmonella, which is why they are a popular choice within healthcare settings.
Viruses too, can cause a wide variety of illnesses. One of the smallest known non-enveloped viruses, Phi-X174, is used as an internationally recognised standard in anti-viral testing to analyse the resistance of critical PPE and air filtration systems to blood-borne viruses. Non-enveloped viruses are much harder to kill because they carry the proteins used to infect cells in an inner layer which is less susceptible to disinfectants. This is in contrast to their enveloped counterparts which have an outer membrane. The membrane contains the proteins used by the virus to enter its victim’s cell and is sensitive to chemical and physical treatments. Because non-enveloped viruses are harder to disinfect, it is one of the reasons why protection against Phi-X174 is used as a standard for evaluating anti-viral performance. Both our Logic Plus and MK Base ranges have been tested in accordance with ISO 22196: 2011against the Phi-X174 virus, with kill rates of over 99.99% and 99.99% respectively2.
Health and safety are at the forefront of workers minds now, and looks likely to remain high on their agenda long even after the pandemic ends. By investing in their building’s infrastructure and using solutions that will help to provide a healthier and safer environment, companies can potentially differentiate themselves for staff retention and recruiting, and make their spaces more attractive to customers and other users. In the long-term, this may also have a positive impact on the real estate’s value, resulting in a win-win for all stakeholders involved.
1 www.nhs.uk/conditions/mrsa
2 Honeywell data on file
Emma Segelov is EMEA marketing operations manager at MK Electric