Start planning now for Part L changes
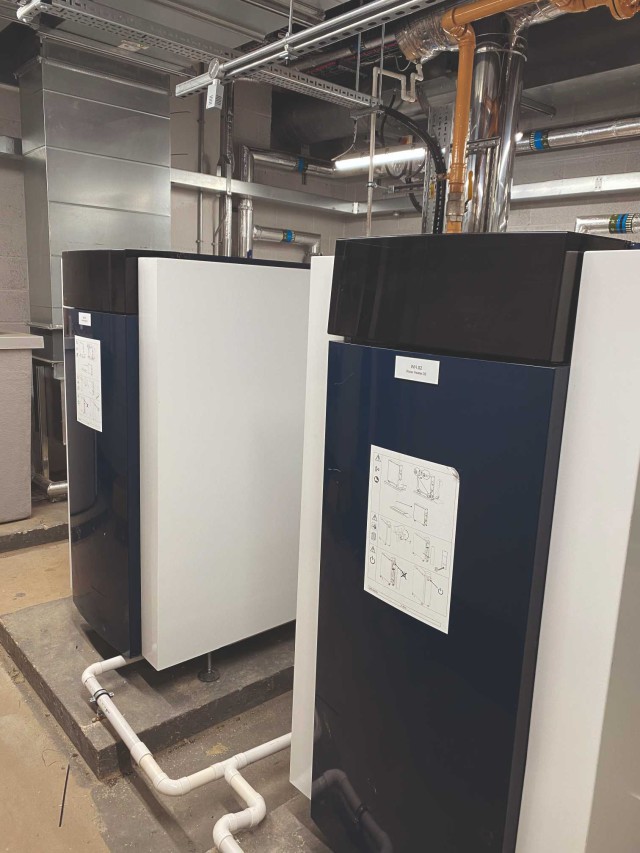
Changes to Part L of Building Regulations are set to rule out non-condensing water heater replacements from 15 June this year in favour of more energy-efficient condensing units. Baxi’s Technical Director Andy Green looks at the implications for Building Services professionals and why it pays to plan ahead
In just three months’ time, tighter water heater efficiency standards will effectively remove the opportunity to carry out like-for-like non-condensing water heater replacements in the vast majority of non-domestic buildings. How can building services professionals ensure that businesses are protected moving forward? Our advice is to encourage proactive planning now to future proof the hot water system.
Stricter efficiency standards
Back in December, the government published its much-anticipated changes to Building Regulations. Five revised Approved Documents were unveiled in total, including Approved Document L which is concerned with the conservation of fuel and power in existing non-domestic buildings. One of the uplifts within the document relates to tighter minimum thermal efficiencies for dedicated domestic hot water heaters.
The new requirements require direct-fired water heaters to achieve a minimum heat generator seasonal efficiency of 91% (GCV) for natural gas and 92% (GCV) for liquefied petroleum gas (LPG). For indirect-fired water heaters, the minimum heat generator seasonal efficiency is set at a minimum seasonal efficiency of 91% (GCV) for both natural gas and LPG. The new standards, which will apply to both existing and new non-domestic building stock, will come into force from 15 June 2022.
What does this mean in practice? In essence, the more stringent efficiency standards will phase out the use of non-condensing water heaters in the vast majority of buildings.
Are there any exclusions? Approved Document L notes that in very exceptional circumstances, where condensing water heater replacement is deemed not suitable or practical by the Building Control Body, a minimum seasonal efficiency of 80% for gas, or 79% for LPG may be used.
Condensing vs non-condensing
Direct-fired water heaters are well established as providing an efficient, cost-effective means of delivering large volumes of sanitary hot water in a short time. Hospitals, hotels and leisure centres are just some of the organisations with a high demand for instantaneous hot water that rely on direct-fired water heaters to meet their requirements.
Currently, most manufacturers and suppliers offer a choice of condensing and non-condensing models.
Condensing water heaters, unlike non-condensing varieties, can capture and re-use latent heat that is otherwise lost through the flue. As a result, they are up to 20% more efficient than non-condensing models. Units like the Andrews Water Heaters ECOflo, MAXXflo EVO and SUPAflo EVO, for example, can achieve near maximum efficiencies of up of 98%. NOx emissions are also lower, making them the natural, sustainable choice in new build premises.
But a significant number of businesses still rely on non-condensing water heaters to provide hot water services. What’s more, at present, there is still the option to carry out like-for-like replacements of non-condensing water heaters. The advantage of this rapid, easy-fit approach is that no major work is involved, so the equipment can be replaced quickly with minimal disruption to the daily operation of the building.
The disadvantage is that some businesses consequently fail to upgrade to the more efficient technology and so miss out on the energy, cost and emission-reduction benefits from the more energy-efficient equipment.
Hence the government’s stick to rule out non-condensing water heaters. Introducing more stringent minimum efficiency standards is part of its roadmap to drive improved efficiency in buildings and achieve a net zero economy by 2050.
Additional planning
Given that water is a critical service, what will the changes mean in practice for businesses and organisations?
While the benefits of switching to more energy efficient technology are clear, certain factors will require additional planning.
Take the flueing arrangement. A traditional non-condensing water heater will typically require a vertical flue that will go from the plantroom through the roof. Subject to installation standards and requirements, there may be the option to line the existing flue rise when replacing a non-condensing unit with a condensing water heater.
However, on many projects, a complete replacement flue system is likely to be required. One solution might be to replace the complete flue rise with a horizontal flue which would go straight through a close outside wall. This will be dependent on adequate wall space and the terminal position meeting the following standards and guidance notes: BS5440: Flues and ventilation for gas appliances of rated input not exceeding 70kW (net); IGEM UP 10: Installation of flued gas appliances in industrial and commercial premises; Building Regulations Part J Section: Additional provisions for gas burning appliances with a rated input up to 70kW (net). Experienced hot water solutions providers will also be able to advise on the best approach.
A second consideration is the condensate. Condensing water heaters, unlike non-condensing models, require a suitable drainage point to discharge the condensate that is formed in the normal operation of the unit. While there may be a condensate discharge point close to the installation, an alternative location may need to be identified if this is not available.
Both factors will need to be assessed on a project-by-project basis.
Proactive asset management programme
Given these added considerations, how best can we support facilities and estates managers and building operators and help them prepare for the changes ahead?
Our advice is to start working with them now to implement a thorough asset management programme. With regular condition surveys and plant asset inspection in place, they will be sufficiently informed to plan ahead to future proof their hot water systems.
Switching from a reactive to a proactive approach will enable them to prepare for change and budget ahead for future upgrades, thereby avoiding emergency situations and protecting their business.
Even on the few and far between projects where exemptions may apply, forward planning is no less essential. Early engagement with the Building Control Body will be critical if contractors are to ensure that they are satisfied with the recommendation and avoid any risk of censorship.
Achieve longer-term goals
Enforcing condensing water heaters might be a governmental stick to drive improved energy efficiency, but, moving forward, the ‘carrots’ or benefits for building operators are intended to outweigh the challenges. A reduced carbon and NOx output will put a firm tick in the sustainability box while significantly lower running costs can only be welcome at a time of rising energy prices.
Collective support by contractors, specifiers and manufacturers to implement proactive planning might also provide just the encouragement that is needed for some businesses to tackle the heat decarbonisation challenge.
For operators of the UK’s notoriously harder to heat buildings, the energy transition is unlikely to happen overnight. But upgrading from non-condensing to condensing water heaters could be the all-important first stage in a stepwise refurbishment programme. A natural progression, where budgets permit, would be to integrate air source heat pumps with condensing water heaters in a hybrid system. This would reduce the carbon footprint still further by meeting the hot water demand more sustainably.
Working together
What nobody wants is for buildings to be left in an emergency situation with no hot water supply. And if organisations are to protect their business operations moving forward, they need to start implementing a robust upgrade plan now or run the risk of potentially costly, extended downtime and disruption.
As manufacturers, we look forward to supporting contractors, specifiers and end users with site visits, assisting with sizing and helping assess the challenges and opportunities to achieve the most appropriate solutions at the right time. By working together, we can encourage businesses to plan ahead to achieve a smooth transition to a hot water system that is simultaneously more sustainable and future-proofed – and in so doing minimise disruption and help protect the bottom line.
Andy Green is Technical Director at Baxi