AHU design and operation, a modern approach
Adam Taylor, CEO at ARM Environments, explores the two main reasons why HVAC systems cost more than necessary when it comes to energy use and planned maintenance.
Firstly, when AHUs are procured, particularly via the Design and Build route, minimising the ongoing maintenance and running costs for the AHU is normally less of a priority than lowest initial CapEx costs at tender stage. Even with the traditional design route, consultants with the best intentions are often asked to compromise on measures that will perform better in the long term, for those that are initially cheaper.
Secondly, once a building is in the operational phase of its life, FM contractors who maintain the HVAC systems may not have the same priorities as the end client. Billing regular site visits and consumables is better business for them than investigating how much can be saved by looking at a holistic change to the way the existing HVAC is operated and maintained. Their limits of expertise may also mean that they won’t directly be able to offer clients the fan upgrades/optimised filtration and Indoor air quality sensors required to achieve the maximum energy savings possible.
Guidance for specifiers and building owners
We aim to guide specifiers and building owners through available options that specifically suit the way their building is or is due to be operated.
There are battling priorities for building operators at present. A rapid increase in awareness around the importance of air quality is driving building operators to provide higher ventilation rates and better quality air. This, when delivered with a standard ventilation system will increase energy use and maintenance requirements. It is possible to optimise HVAC systems to provide good indoor air quality without using too much energy, but it does involve taking a deep look at the HVAC design.
There are two main aspects of an air handling unit that will affect how much energy it uses, the first is the grade of filtration. The second is the efficiency of the fan and motor driving the air flow. While these items can be looked at in isolation, it is best to take combined approach when looking to upgrade an air handling unit.
Standard filters in air handling unit systems are primarily designed to protect and keep the ductwork clean, and typically selected on a rule of thumb basis (G4 prefilter/F7 Final filter in old money EN779 terminology) rather than selected to provide a particular quality of air. The grade of filters required depends on the outdoor air quality, see Eurovent REC4-23 for guidance1. It is possible to gather local air quality data to feed into selection software when modelling a filters’ longevity or selecting the appropriate grade.
Unfortunately, the type of filter used in an air handling unit is normally chosen based on initial CapEx only with no regard of the OpEx costs of that filter both in terms of replacement intervals, the labour to change, nor the energy used by that filter as it starts to clog.
There is an industry-wide assumption that filter grades cannot be upgraded in air handling units because of an inevitable increase in pressure drop. In the example shown in table 1, we demonstrate that both the filtration efficiency can be increased at the same time as reducing the pressure drop by using a different specification of filter.
Based on the selection shown in table 1, based on current energy costs, the annual energy cost for the filters in scenario 1 is £9,630, for scenario 2, the energy cost is £6,289. It is important to highlight, that despite the higher energy efficiency, the filters selected in scenario 2, are a higher grade, and offer superior filtration performance.
See table 1. Bag filter comparison – 2” panel and E rated 535mm ePM1 60% 8 pocket bag vs. 2” panel and A+ rated ePM1 85% 10 pocket bag.
Standard bag filters with low numbers of pockets are cheaper (~£25) than long life mini pleated ECO filters (~£70), but the latter has a higher dust holding capacity. For PM1 it’s 41g vs 68g, and for PM2.5 it’s 57g vs 89g, so the ECO filter will last longer, resulting in reduced maintenance visits.
See table 2. Compact filter comparison – 2” panel and E rated 535mm ePM1 60% 8 pocket bag vs. 2” panel and A+ rated ePM1 60% compact filter.
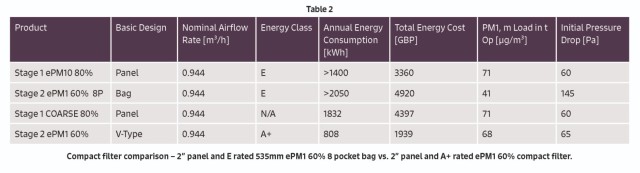
The additional saving in the compact filter comparison shown in table 2, comes from the lower initial pressure drop of the compact filter (145Pa vs 65Pa). This results in an energy saving of £1584 (18.5%) between the two selections.
It will be difficult to realise the full potential cost savings if the maintenance regime is not altered to match the new filters. The unknowns surrounding when to change a filter means that many filters will either be changed too often or too infrequently. Few AHU’s have working pressure drop sensors fitted to them. They may have magnehelic gauges in the plant room, or on the roof but these are not regularly checked, as this requires an expensive specialist visit. Pressure differential sensors can be connected to the building management system to alert of a required filter change, but there is then a time-lag before replacement while the filters are operating inefficiently. A stand alone AHU monitoring system communicating to the cloud via a 4G gateway can be provided so that both the filter status and AHU run-time can be monitored remotely. Attendance on site to change the filters is therefore only required when the filter has reached the point where it's dust loading and therefore pressure-drop makes it more economical to change. This brings savings in material use, labour costs and energy.
Reduced occupancy in buildings is for the time being, the new normal
It is no longer appropriate to use the same filter change intervals as it was three years ago. It's more important than ever to know the quality of the air and the amount of it that is being brought into the building. By measuring the air flow through the filters and correlating that with the outdoor air quality at the time, it is possible to model the dust loading of the filter so that they can be scheduled to be changed at an appropriate time. In a building where the workers are now running a hybrid working strategy, filters that were previously changed every three months could potentially go six to nine months without replacement in a building with demand controlled ventilation.
Doing away with routine planned maintenance for filters only provides minimal labour savings when the FM teams still need to regularly inspect the belts on the fans in the air handling units. By simultaneously changing to direct drive fans, the need to regularly replace fan belts is removed. Modern fan motors can measure and report their status in terms of torque, power consumption, vibration etc to either a BMS or to a remote software platform via a 4G gateway. While we would recommend using 4G gateways to transport the data to the cloud, all of these monitoring systems can be directly connected to the building management system if data concerns exist at critical sites.
Older style centrifugal fans may have been optimised for delivering high pressure with forward curved blades. Modern backward curved fans are more efficient and quieter, the motors that drive them have come a long way in just the past ten years, with far more efficient systems now available. Mixed flow fans combined with a replacement fan wall, will offer the biggest energy savings in certain situations.
The choice of which style of fan to use is dependent on how the building is to be operated, EC fans are highly efficient at their design duty, but do not give the same energy savings at lower speeds as the latest switched reluctance motors. Because of this, it is important to understand whether the ventilation system is demand controlled or operates at reduced fans speeds for large portions of the time or, if the system is typically running at a constant ventilation rate. This will help define which style of fan upgrade is most appropriate.
This step change in maintenance requirements can be demonstrated via a return-on-investment calculation that takes into account both reduced energy from more efficient fans and filters plus, the reduced site labour costs. ROI when changing to a cloud-based maintenance and operation strategy is significantly shortened where travel times are longer or there is a high level of security at the site causing access challenges.
Further considerations
To derive real value from an AHU upgrade, it's important to consider all aspects of the refurbishment. If replacing coils, fitting UVGI systems on the downstream side of the cooling coil will keep the coil surface and drain pans free from biofilm build-up further reducing the need to regularly inspect coils and drain pans. Further energy savings are realised by reducing biofilm build-up, as this keeps the cooling coil working optimally by ensuring efficient heat-transfer.
Combining upgrades to air handling units in combination with adding in-room, or in-duct indoor air quality monitoring sensors allows for further enhancement opportunities. The addition of IAQ monitoring allows for air quality improvements to be made without wasting energy, as the ventilation rates can be altered according to both CO2 and other indoor pollutant concentrations.
- https://tinyurl.com/59fh8pez