‘Tis the season to be commissioning

Stewart McGillivray, Seasonal Commissioning Manager for Guardian Water Treatment, explains the steps maintenance teams need to take to ensure buildings work as they were intended.
During the winter months, an essential heating and ventilating plant has to work hard to keep occupants warm. Comfort is a priority, balanced with ensuring energy efficiency to combat rising fuel bills.
Despite it still being very mild at the end of September, that was the time that maintenance teams and financial managers needed to begin preparing for the essential seasonal commissioning tasks that ensure buildings in their care are ready for the increased demand on heating. These activities contribute to ‘soft landings’: the process of maintaining the design brief of a building and ensuring it performs as it was intended, with a focus on optimal comfort and functionality for occupants.
Seasonal commissioning should take place throughout the year with thermal comfort, ventilation and lighting all checked using measurement and occupant feedback. Where buildings have changed their heating or air conditioning technology (such as switching boilers and chillers for heat pumps) seasonal commissioning is particularly important to prove the new capital plant performance.
During the winter, the focus obviously moves away from cooling to heating, checking optimal space temperatures, heating plant flow and return, energy consumption and BMS trends. The design values of the scheme are used as a benchmark. Any works that have been carried out in between seasonal commissioning periods should have been logged so their impact can be checked.
FMs are often contractually obliged to maintain climate conditions and prevent downtime, so seasonal commissioning is crucial to preventing liability cases. Buildings that are too hot or too cold can lead to commercial spaces becoming unfit for occupation, especially in multi tenanted offices.
Let’s not forget that heating and cooling is not just for people. Many commercial sites require very specific temperature control for their operations, for example data centres, pharmaceutical environments, manufacturing facilities and food storage locations. In these examples, faulty HVAC and/or control strategy can lead to very expensive issues.
Seasonal commissioning shortcomings
A ‘soft landings’ clause is often written into contracts but because of the shortcomings of seasonal commissioning, it is sometimes hard to achieve.
Common challenges include:
- Hidden mechanical issues: Problems within closed-circuit water systems often go unnoticed until it is too late.
- Corrosion: One of the biggest threats to HVAC systems, corrosion silently erodes pipework, leading to costly repairs and downtime. Corrosion can occur at any phase of a building’s lifecycle, from pre- commission to ongoing operation.
- Extreme weather conditions: These can lead to malfunctioning temperature control systems, causing disruption and downtime.
- Accurate measurement: The objectives of ‘soft landings’ can be difficult to quantify.
- Loss of building knowledge: High staff turnover can result in a deterioration of building knowledge and failures within the ‘soft landings’ process. Ongoing training and support for FM teams should be a central part of the strategy.
Closed systems in particular suffer from the first two challenges. At the point where a problem (usually caused by corrosion) reveals itself, it is likely to be very costly and disruptive to rectify. Leaks in the pipework, for example, mean corrosion has been there for some time.
Monitoring = transparency
Thankfully, in our now data-driven world, there are tools available that can remove the guesswork from building services. A building management system (BMS) is part of this jigsaw puzzle and keeping a good handle on trends, while tweaking functionality to meet seasonal demands, plays an important role in winning the ‘soft landings’ battle.
There is also monitoring technology specifically designed for closed systems, checking a range of parameters indicative of corrosive conditions and providing early warning of potential problems. The word ‘potential’ is key here, as by jumping on changes well before the visible issue appears corrosion and its symptoms can be stopped in their tracks.
Oxygen levels, pressure fluctuations, pH, inhibitor levels and galvanic currents, for example, all provide clues as to what is going on behind the scenes. These indicators are essential weapons in the seasonal commissioning arsenal and show that microbiologically-influenced corrosion (MIC) is not active.
Technology delivers readings every 15 minutes, 24/7, which means that when seasonal commissioning comes around, there is less intervention required as those responsible can be certain of closed-system condition.
Where disruption has occurred, as demonstrated by reviewing the monitored data, or where changes have taken place as a result of adjustments in usage, ongoing monitoring can show the success (or failure) of these activities, accurately pinpointing cause and effect. Where liability cases do arise, this accuracy can prevent false accusation of responsible parties.
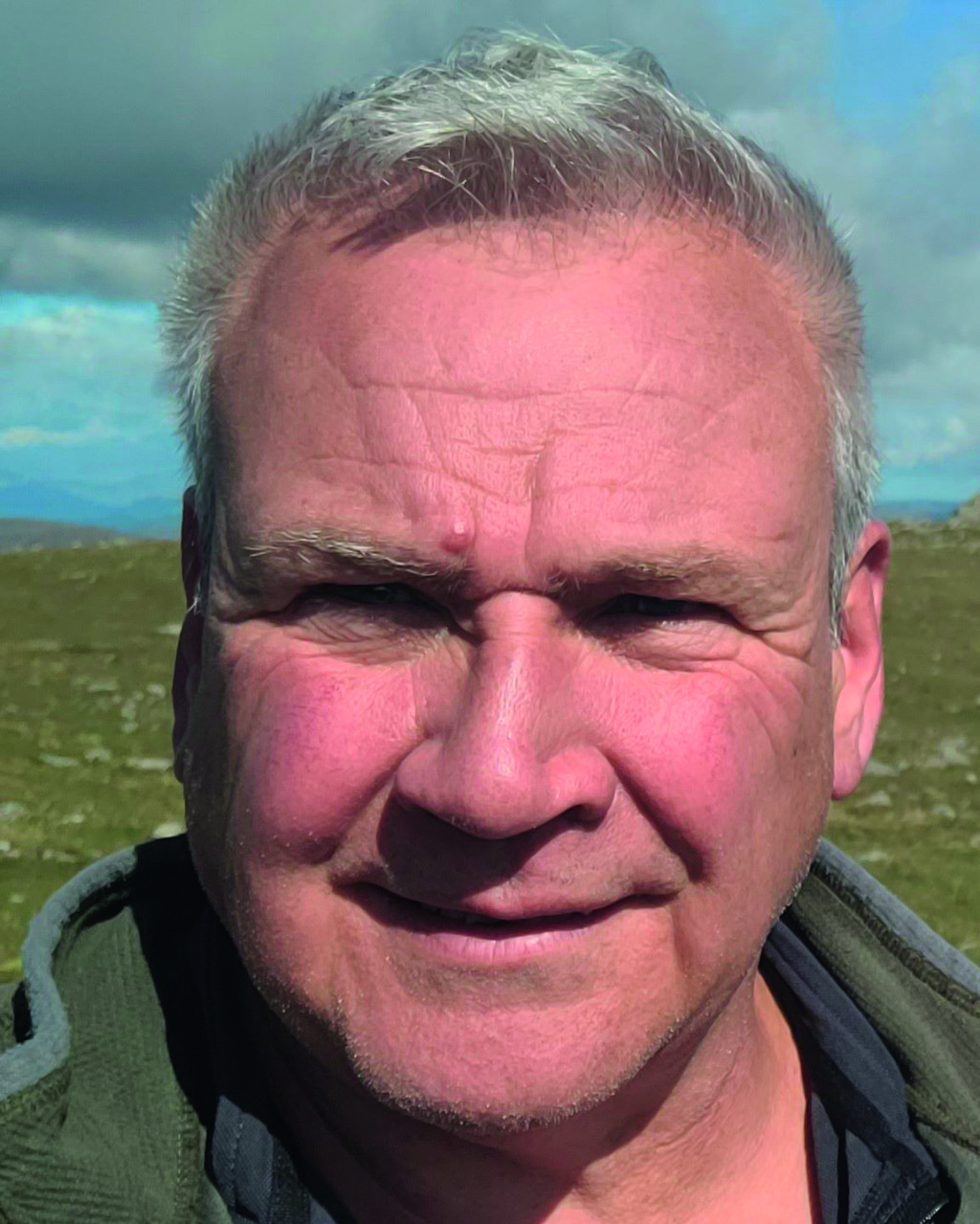
Overall, where a closed-system is only tampered with when there is a problem, more sustainable and cost-effective maintenance practices ensue. Knee-jerk reactions, such as flushing and dosing, can be avoided, reducing water wastage and preventing the overuse of chemicals. Less time is spent on site and the use of off-plan external contractors is limited.
In general, monitored HVAC works better and lasts longer, improving whole-life costings.
In addition to monitoring, there are other factors that will improve the effectiveness of seasonal commissioning:
Strategy: To enhance desired outcomes, a clear strategy should be in place, involving close collaboration between all key stakeholders, including designers, contractors, and facilities managers.
The strategy should focus on the key areas which soft landings should be measured against, as detailed in BSRIA guide BG74/2019:
• Energy consumption
• Economic or financial need
• Social and well-being need
• Sustainability and environmental aspect
• Functionality
Training: Everyone involved in the usage and maintenance of temperature control equipment must have training, including maintenance teams and end-users. Filming training is a great way to pass on knowledge to new staff.
Loss of building knowledge is one of the most common reasons that the ‘soft landings’ process breaks down.
No more hidden surprises
Building services and the people responsible for them are under a lot of pressure, juggling end-user comfort, rising fuel prices, operational certainty and in some cases, supporting conditions that allow extremely valuable technology to operate or safeguard essential products. The stakes are high.
Real-time monitoring of hydraulic closed-systems, alongside clear strategy and knowledge sharing, is essential for successful seasonal commissioning, dramatically reducing the risk of major issues and subsequent liability.