The Tek screw timebomb

Airmec Essential Services Managing Director Andrew Steel details the planning of a practical response to the fire damper installation warning.
Annual inspection of fire dampers is required to meet the requirements of BS999: Code of practice for fire safety in the design, management and use of buildings and where adequate inspection hatches have not already been fitted, building owners and managers have been facing unexpected expenditure which can leave a big hole in the FM budgets.
We are now waking up to another ticking bomb; The use of steel self-drilling (Tek) screws to install fire dampers in the first place.
Let’s assume that designers and installers did what was necessary by following manufacturer instructions in good faith. However, the majority of installations we see have ductwork connected to fire dampers using steel self-drilling screws. The installers may have made savings by having a speedier installation, but you are going to have to fund the remediation work.
The issue has been flagged up by the Building Engineering Services Association, which says that maintenance contractors carrying out annual inspections have found that “a huge number of dampers” had been incorrectly installed, presenting risk that cannot be ignored.
The call to action
It’s now necessary to ensure there is an up-to-date survey for fire dampers, and plan remedial works as necessary.
It’s work that involves multiple skill sets. It cannot just be tagged on to the routine annual inspection and drop testing. The person who can survey and report on the condition and installation of a fire damper infrastructure is not the same as the technician who will typically undertake the routine inspection, testing and cleaning of dampers.
Their proficiency levels and hourly rates are vastly different. Rather than panicking however, take the opportunity to scope and price the work properly. Any remediation contract will base estimates on an hourly rate, so it’s important that the team your partner fields brings the right combination of skills to the table in the right ratios.
What might the outcome of a survey be? Ideally a clean bill of health. If not, incorrectly-fixed dampers can usually be refitted using required fusible fixings for a fraction of the cost of replacing a damper from scratch. Re-fixing work would be followed by a suitably qualified and registered passive fire protection specialist verifying the correct fire stopping system has been applied and correctly installed. Only then comes the return to routine annual inspection, testing and resetting of the fire damper.
Don’t be fooled by the fact that dampers have apparently passed muster before. A damper with the wrong fixing screws could be in good working order and pass annual routine inspection and testing but if it has the wrong fixings, it may well not perform in a fire.
Work with your service contractor to build a matrix of tasks to be carried out and identify the skills needed to do them. All of this should be based on a judgement of the risk attached of the various issues.
The problem
‘The current concern surrounds the use of the wrong type of fixings, self-drilling or Tek screws, to fix ventilation ductwork to dampers.
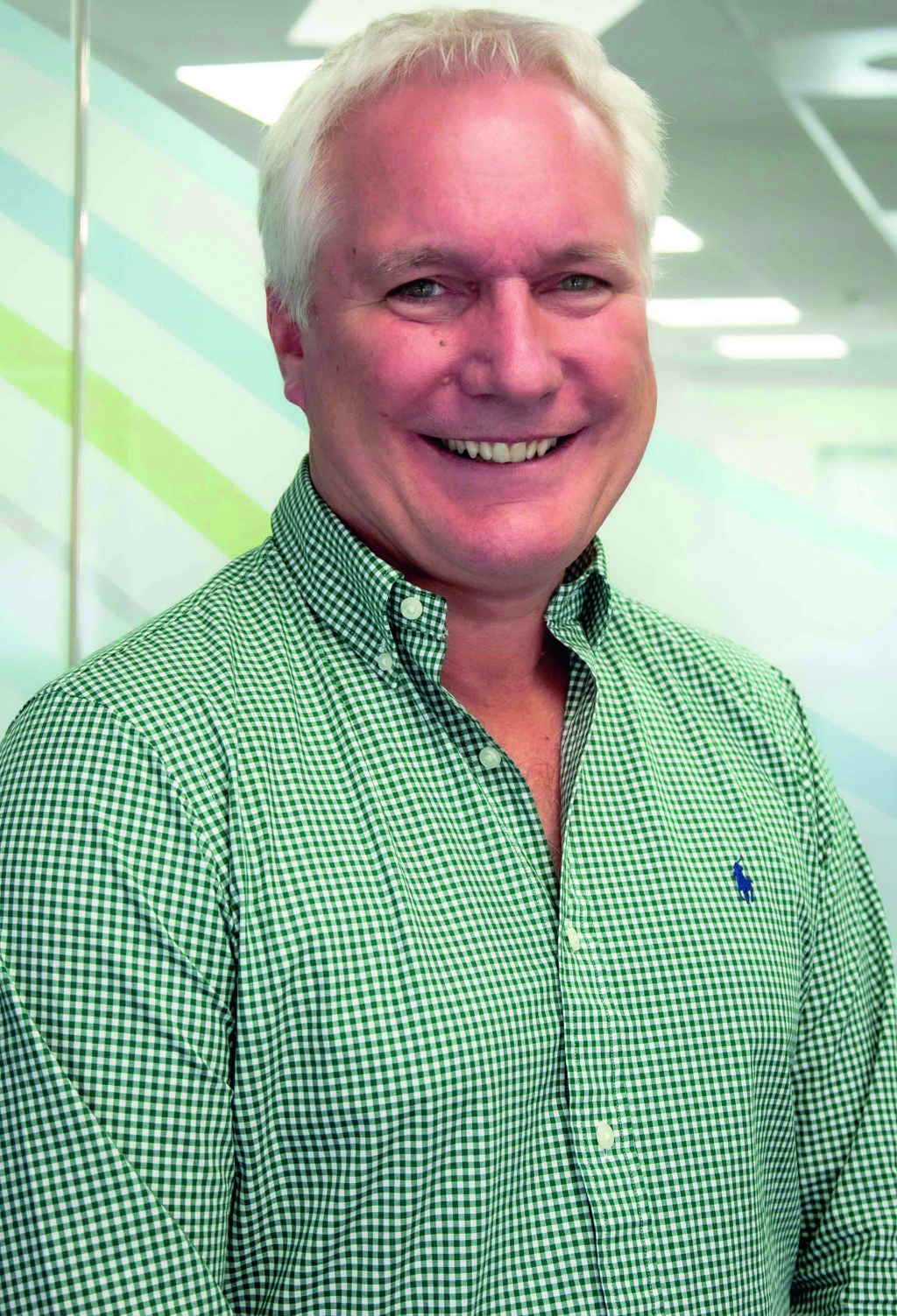
As fire damper inspectors and testers, we can attest to having seen enough instances of this to know the issue is a real and live concern, although no- one knows for sure how common it is. So, you need a strategy for checking all your dampers and scheduling remedial work as necessary.
Correctly-installed dampers must be secured by fixings such as aluminium or nylon, that melt in a fire and allow the duct to break away, otherwise a collapsing duct could pull the damper out of place and break the seal between the fire zones.
Why now?
We in the services industry have been successful in boosting the uptake of fire damper testing and inspection across all industries, and that has eventually led to there being a critical mass of feedback on the use of inappropriate fixings. The issue cannot now be ignored and, quite rightly, the industry itself is pushing it to the forefront.
The alarm bell was sounded last year by The BESA (Building Engineering Services Association), and the strength of the warning has successfully precipitated government action from the UK’s product regulator, the Office for Product Safety and Standards (OPSS). OPSS says it has contacted some manufacturers, importers or distributors of smoke control dampers asking for documentation which includes, but is not limited to, declarations of performance.
BESA is updating its own guidance which will presumably spell out chapter and verse on how fire dampers should be fitted. The new guidance Is expected later this year, but BESA has already issued an Interim technical note on fire damper maintenance to stress the importance of using the correct fixings for dampers. Be under no illusion: Incorrectly-installed fire dampers may well not perform their function of reducing the spread of smoke in a building during a fire. You need to act now to check on your installation.
The guidance
There are multiple statutes for fire dampers. At the top of the regulatory tree is The Regulatory Reform (Fire Safety Order) which requires that the person responsible for the building (be that the owner or the occupying employer) takes necessary precautions for fire safety in a building.
BS 9999 is the recognised Code of Practice for fire safety in the design, management and use of buildings and it requires that fire and smoke dampers are tested annually. Any dampers found to be faulty must be repaired or replaced on an urgent basis.
At a practical level, it is BESA DW145 – Guide to good practice for the installation of fire and smoke dampers and BESA VH001 – Fire damper maintenance which are the touchstones. VH001 3rd edition requires confirmation of the presence of breakaway and flexible joints that will leave the damper in place and maintain fire separation if there is a fire.
Who is responsible?
There are a lot of people involved in fire damper specification and installation but overarching all this is the previously-mentioned Regulatory Reform (Fire Safety Order) which states that it’s the responsibility of the person in charge of the building to take necessary precautions.