Fire damper installation
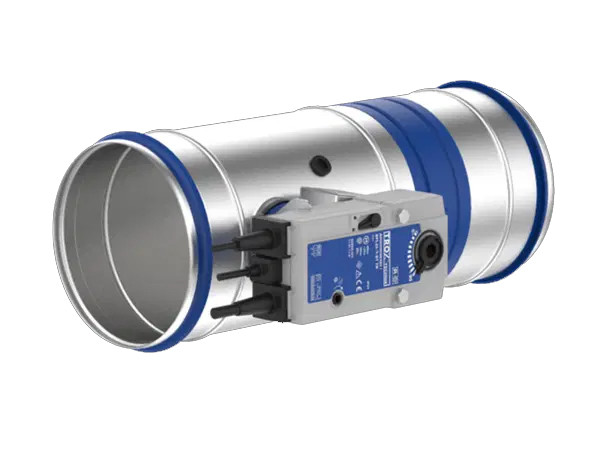
Mike Gosling TIFireE, Technical Director at TROX UK, looks at the new guidance for meeting Building Safety Act 2022 requirements.
In 2021 the latest figures from BSRIA estimated that around 146,000 mechanical curtain dampers and 70,000 motorised dampers are installed every year. These are for new builds and replacements, which accountfor just 1% of the annual market, suggesting that the total number of dampers already installed in UK buildings could be as high as 100 million. There is evidence to suggest, however, that only a small proportion of these are meeting regulatory requirements with respect to regular inspection and maintenance.
Since the publication of the new Building Safety Act 2022, a significant amount of secondary legislation has been introduced, and those of us involved in the design, manufacture, installation and maintenance of fire dampers for air conditioning systems had been waiting for publication of new guidelines for some time. These are now available in the National Association of Air Duct Specialists fire dampers guidance document (NAAD-22).
What are the key changes coming out of the Building Safety Act 2022 in regard to fire dampers?
An important change is the requirement now placed on individuals designated as Accountable Persons and Duty Holders to carry out weekly as well as (at least) annual checking/testing regimes on fire dampers. These are clearly defined in the new NAAD-22 guidance document. Under the Building Safety Act 2022,certain categories of building are designated as Higher- Risk Buildings. These include buildings more than 18m in height, or with at least seven storeys. Hospitals, care homes and buildings containing at least two residential units also fit within this category. All existing buildings in this category were required to be registered with the Building Safety Regulator by 30th September 2023. From 1st October 2023 all new builds categorised as Higher-Risk Buildings are required to be registered with the Building Safety Regulator prior to occupation. The testing regimes for fire dampers are dictated by the categorisation of the building involved, with additional responsibilities for those designated as Higher-Risk.
What are the key points of the new NAAD-22: Fire Dampers Guidance Document?
The NAAD-22 document covers design, selection, installation and maintenance of fire dampers. It is available for free download at https://www.naaduk.co.uk/naad22-guidance-document-app/.
In addition to providing an overview of damper types, NAAD- 22 provides guidance on minimum regulatory requirements for routine maintenance, testing and inspection of installed dampers.
It also covers installation, testing and commissioning of dampers during initial installation, as well as considerations for the correct design for, and selection of, fire dampers. Some key areas to study are the requirements relating to system design and damper selection, and the importance of detail and quality of workmanship during installation.
As an example, the person designing and selecting the fire dampers should understand:
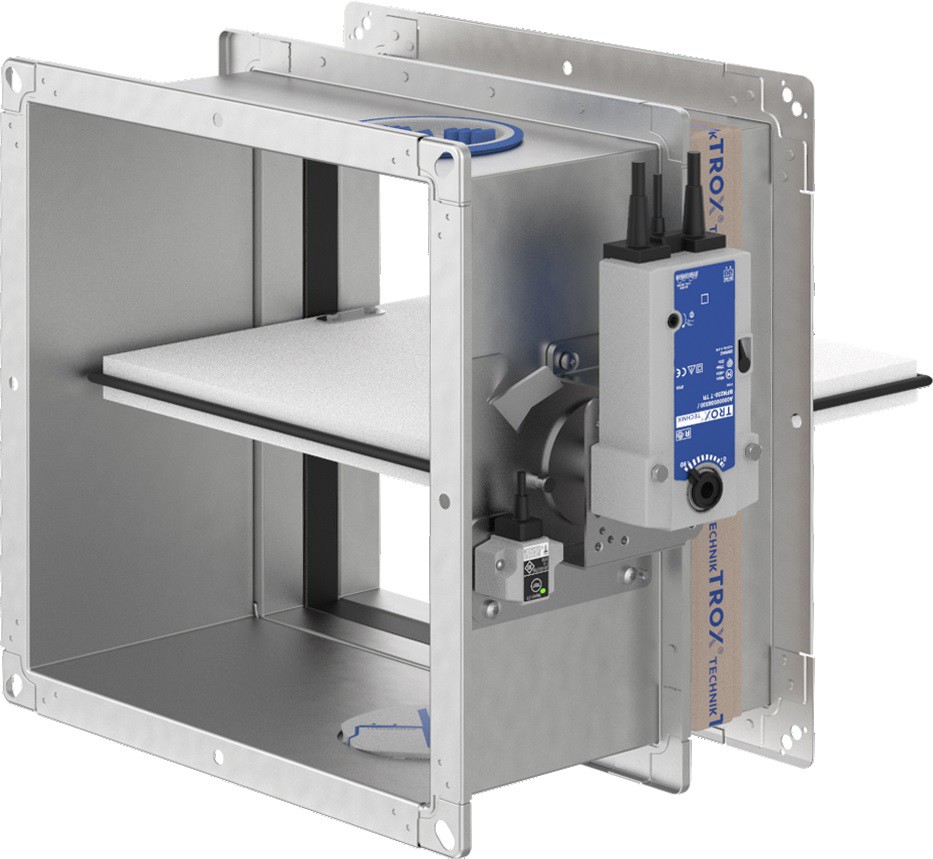
- The principles of compartmentation
- The standards and principles for testing FDs and SCDs
- The applications of FDs and SCDs
- The correct procedures for the selection and installation of FDs
- Building services spatial coordination
- The correct procedures for access to, regular testing, maintenance etc for FDs
- Demonstrate good behavioural and ethical competence
Recognition is given that the required knowledge may not be held by a single party, therefore, the involvement of a manufacturer at the early stage of design, who can support the Dutyholder with respect to the certified applications of the dampers, should be considered.
In the case of a new build, once the building has been designed for compartmentalisation, and the damper is being selected, the type of supporting construction into which the damper is to be installed is crucial. The manufacturer must provide a Declaration of Performance (DoP) and Installation & Operating Manual (IOM) to the Dutyholder, ‘specific to the supporting construction’. Without both of these documents, there is no guarantee of performance that the installation will meet the required performance.
Engagement with the fire damper manufacturer at an early stage is crucial to achieve compliance.
Failure to install a fire damper in accordance with manufacturers’ IOM, without obtaining permission for an installation deviation, will render the fire damper non- compliant, with responsibility to underwrite the installation falling on those involved in this design decision. After installation, changes to the building use which might impact upon the required damper classification are also critical, as they could void the original installation compliance.
What help can manufacturers of fire dampers provide to those specifying and installing fire dampers?
Engagement with the fire damper manufacturer at an early stage is crucial to achieve compliance. With one of Europe’s most modern fire protection laboratories, the International Centre Fire Protection Technology (ICB), TROX has developed its range of fire dampers for a wide range of supporting constructions encountered in modern buildings from solid walls and floors to lightweight partition walls (metal and wooden stud), solid wood/CLT walls and floors, sandwich panel walls, asymmetric shaft wall, ribbed concrete and hollow deck, among others. This has resulted in third party Notified Body testing and certification of over 400 damper installations. So we can assist those specifying dampers by providing proven, declared performance within an extensive range of supporting constructions and with multiple penetration seal options.
TROX has developed training seminars on fire damper and smoke control damper testing, classification and installation. TROX also supplies four fire damper variants to meet the requirements of varying system designs, all of which conform to the harmonised product standard (BS EN15650), have been tested to BS EN1366-2/BS EN15882-2 and classified for integrity (E), insulation (I) and leakage (S) to BS EN13501-3.