Taking control of energy performance

Sonia Bajwa explains how controls can be used to reduce energy consumption and associated costs in buildings — and looks at what the considerations for building managers are.
Energy is generally thought of in terms of cost, and new legislation will have a direct business impact on energy use. With this in mind the Carbon Reduction Commitment is something that a lot of organisations are gearing up to. The tax, which will come on line in 2010, will become an additional cost to the Climate Change Levy that is already in effect. Good energy efficiency can help to reduce these charges, in conjunction with the running costs of the building itself.
An Energy Performance Certificate (EPC) is now required for any building that is for sale or lease. It provides an energy rating based on the building design and includes a report that makes recommendations for improvement. Energy performance is one of the factors that may help to secure the sale or lease of a property during the credit crunch.
Communal public buildings such as schools, libraries and local authority buildings over 1000 m2 now require a Display Energy Certificate (DEC) that indicates the building performance in relation to carbon-dioxide emissions as a result of energy consumption. An EPC or DEC can prove a valuable marketing asset, helping to demonstrate lower running costs to potential customers.
Lighting, heating and cooling, ventilation and other building systems require good management to keep their energy consumption systems under control. The Carbon Trust estimates that 90% of all building controls are inadequate, costing UK businesses over £500 million every year in unnecessary energy costs. This equates to a high level of additional CO2 emissions that could otherwise be saved, with the knock-on effect of reduced taxation levies, lower running costs and improved comfort conditions for building users.
Building controls play an important part in the running of the building’s systems, provided they are fit for purpose. That is, they need to be suited to controlling the plant and meeting the organisation’s activity needs. Programming is important to accommodate periods of down-time such as weekends and bank holidays.
Controls need to be optimised according to the nature of the building and the organisation that is using it.
The requirements of a school will differ greatly to those of an office in terms of the hours of lighting and the amount of heat required, depending on the size of the buildings.
The system should be installed with sufficient sensors and monitoring to ensure that different areas of a building are catered for. Effective zone controls, particularly for energy consumption and performance improvement, can achieve efficiencies and cost savings on energy use. The uses to which different areas of the same building are put often mean that their energy requirements can differ greatly. For example, the requirements in offices will vary from those in factory or operational areas where specialist lighting and machinery is used.
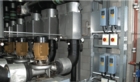
Intelligent controls allow a system to learn to match demand patterns and respond accordingly. Seasonal variations in temperature, light and energy usage can be taken into account. User adjustability can deliver further efficiencies, as systems with sufficient user outstations provide flexibility to allow the building users to exactly match the building conditions their changing requirements.
When specified, installed, operated and maintained effectively, controls can prevent unnecessary or out-of-hours plant operation across the building, reduce unwanted heat gains in a space from electric lighting or fans and motors, minimise cooling costs and reduce running costs, energy consumption and emissions in general. In the long term, the properly maintained controls or BEMS can reduce excessive wear and tear on building systems and minimise the cost of maintenance, repair and replacement.
Refurbishment presents the ideal opportunity to overhaul the building controls. Ideally when optimising a control system, the plant it controls should also be reviewed and improvements made to ensure this is operating at the best efficiency. For example, fitting variable-speed drives will enhance the overall performance and associated savings.
BEMSs have been in place for more than 25 years but mainly fail to deliver savings because they are not optimised correctly or have been wrongly specified for the application. There can be maintenance issues with the system and the plant it controls with the use of the building in mind. There are organisational issues when plant and control system maintenance is carried out by different divisions of the same organisation. The best energy performance and savings are gained by using a joined-up approach for both controls and plant. Adopting targets for energy efficiency can also help to hone the focus on ensuring that maintenance is not ignored, allowing ‘energy creep’ to cause costs to gradually slide up.
The best examples of BEMSs have optimised control systems and correctly applied sensors that are linked to high-efficiency plant. Coupled with performance parameters for energy efficiency, a single integrated approach to maintenance and the incorporation of BEMSs in the energy-management agenda mean that a building’s controls can be used as an integral part of the energy cost and carbon reduction of a building.
Sonia Bajwa is a sector manager for Dalkia
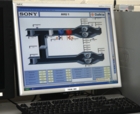