The BEMS as the all-important key to energy-saving environmental control
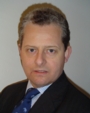
Julian Miller urges the energy manager to look beyond just delivering the right temperatures and think about using the optimum amount of energy to achieve that — and the key is the building energy management system
If I said that 90% cent of heating and ventilating (H&V) systems were inadequate, I’m sure it would lead to a little alarm — and rightly so.
For those who have ever been responsible for specifying, installing, buying, selling or running an H&V system, there is a good chance you may have invested in a bit of a turkey!
Unfortunately, according to the Chartered Institution of Building Services Engineers (CIBSE), this statistic is indeed reflective of the BEMS industry. The CIBSE General Information Report 40, paragraph 1.1 states: ‘It is estimated that 90% of H&V control systems in buildings are inadequate. This costs industry and commerce £500 million per annum in additional energy costs.’
This report was written some 15 years ago, but all evidence suggests that little else has changed. And with £500 million at stake — not mention millions of tonnes of CO2 emissions — it’s clear there is an opportunity to address the situation.
First, it is worth asking what a building energy management system (BEMS) is supposed to do. The obvious answer is ‘to manage energy’. However, the sad fact is that most people charged with operating buildings and their control systems are inadequately trained to do so from an energy perspective. There is, therefore, little hope of meeting the true potential of BEMS unless changes occur.
The reality of most systems is that they are primarily set up to deliver adequate building services (temperature set points, domestic hot water provision etc) and not for energy efficiency. These two objectives, however, are not mutually exclusive.
Quite simply, a BEMS system that has been installed and set up correctly is capable of identifying the demand for heating (or chilling) and should ensure that this demand is met.
A couple of quick pointers; the greater the outside air temperature, the less heating is required and the fewer boilers you need. It sounds logical, but is usually not adhered to by the controls strategy for the building and its systems.
Quite often, a BEMS specification is not fit for ‘energy-management’ purposes. Two questions should be asked.
• Are there sufficient inputs and outputs (IOs) to gain control over the primary plant?
• Can the system identify when boilers and chillers are not needed and turn them off?
Think about it; energy is actually being consumed in the boilers and chillers. From there, it is merely being transported (as hot or cold water) to its point of use at a relatively small additional energy cost. The greatest opportunity for savings is therefore to ensure that the optimum amount of energy is being used at the point of ‘consumption’.
Now let us look at the control over the primary plant. There are thousands of plant rooms where individual boilers are not controlled directly by the BEMS — so they cannot be controlled to their optimum efficiency. Likewise, there are chillers running on their own packaged controls with no reference to what the heating is doing. A lack of connectivity means that boilers and chillers often operate at the same time — hardly a recipe for efficiency.
Is energy being monitored? It’s impossible to manage gas and electricity effectively if they are not being measured regularly. A vast amount of regular analysis can be undertaken very easily with access to meter data. Relating energy consumption to demand by, for example, comparing it with ambient temperature, is a powerful measurement of how well a control system is operating. All too often, this vital element of energy management is overlooked.
And finally, there is the old axiom: ‘If it ain’t broke...’ Energy performance in buildings is not a simple question of right or wrong. It is more complex than that. Rather, look at energy performance as ‘better or worse’, where 100% efficiency is a utopian ideal, but something an energy manager should strive towards.
In reality, so long as the right temperatures are delivered, no-one really knows, or cares, how much it is costing. However, if an energy manager’s role is to care and ensure the optimum amount of energy is being consumed to meet a building’s requirements and also optimising the energy budget, the BEMS, combined with robust monitoring and analysis, is the key tool for delivering these objectives.
What is getting BEMS right actually worth? Fifteen years ago, it was estimated at £500 million, but this is not really meaningful to individual building owners or operators now.
To put it another way, there are few buildings where at least 15 to 20% of the energy for heating, ventilating and cooling could not be saved with a payback of 18 to 24 months. I think that most financial directors would look favourably on an energy-management team that could deliver a return like that. As someone once said, ‘If you reach for the stars, you might just touch the Moon.’
Julian Miller is unity services director at Matrix.