Answering your questions on modular wiring
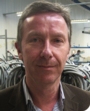
Modular wiring systems are growing in popularity among electrical contractors, specifiers and end-users in the UK, providing significant improvements over hard wired alternatives and reducing on-site installation times by up to 70%. Dave Lewis of Apex Wiring Solutions, answers questions about the technology and the benefits provided.
What is a modern modular electrical wiring system?
The UK’s approach to electrical installations remained relatively unchanged for decades, relying on traditional hard-wired systems, until the advent of modular wiring systems. These have really taken off more recently, and most large-scale capital projects now involve modular solutions. The technology, using advanced quality manufacturing techniques and materials, represents the latest in cutting-edge, cost-effective electrical-installation solutions — a factory-assembled and fully tested cabling system that replaces the traditional wiring of electrical subcircuits.
How does it differ from conventional systems?
The main difference is avoiding the need for any on-site electrical connections. The modular system is designed and produced off-site in a quality-controlled environment. It is then supplied pre-assembled and fully tested to site — rather than the more traditional conduit, trunking and hard-wired system. This eliminates the need for on-site electrical connections and cuts the number of qualified electricians required to carry out installation work, with associated advantages in installation time and health and safety.
What are the advantages of the modular approach?
Modular wiring systems offer a very high degree of flexibility and versatility for both the installer and end-user. They provide improved long-term project performance because the risk element for the installer is reduced, while installation times and the amount of on-site skilled electrical labour are cut. Cable snagging and site waste are also reduced, while offering improvements in site safety. Also, because product is factory assembled in a highly controlled production environment, quality levels are assured.
![]() |
A typical system might feature pre-wired factory-tested pluggable distribution boards for supplying lighting and power over a large industrial site or multi-storey office complex. The use of prefabricated connectors and preassembled cables can provide a high-performance, reliable and flexible wiring solution which offers significant improvements over alternative systems, reducing on-site installation times by up to 70%.
What’s driven the uptake of modular?
The electrical wiring and accessories sector is evolving to meet the challenges placed on it by the introduction of new technologies, the availability of affordable skilled labour and the latest methods of construction such as off-site pre-fabrication, green and lean. So now, during the tough economic conditions we face, not only here in the UK but also overseas, there is more pressure than ever before on everybody within the supply chain to deliver projects on time and within budget — and achieving cost savings in the process wherever possible.
How does the UK market/sector compare to overseas?
The UK has often led the way in pioneering new electrical wiring technologies and solutions. Modular wiring is no different; we are already leading the way in Europe and moving rapidly towards fully integrated systems similar to those found in the more mature markets of North America. Elsewhere, there are nascent markets in places like the Middle East, Asia and Australia where mechanical and electrical specifiers are now beginning to look seriously at the benefits of the modular approach with the adoption of some form of pluggable system.
![]() |
Is modular suitable for any type of installation?
One of the great advantages of modular wiring is its simplicity and versatility, which means in practical terms virtually any installation, regardless of size and complexity, can be converted to a modular system. This includes projects within the residential, retail, healthcare, commercial and education sectors.
Can it be used for smaller-scale projects?
Again, modular wiring’s flexibility means that there is no minimum project size. From single room solutions to the largest multi-million pound new-build hospitals, systems can be either retro-fitted or newly installed to provide users with safe, reliable and convenient power and lighting services.
What’s the specification process?
Most specifications come through a combination of mechanical and electrical contractors and consultants, but we are also seeing building engineers and project managers on some large new-build and PFI developments becoming involved in specifying product.
What’s the best way to install?
Qualified and skilled electricians are generally required to oversee projects, but because components are easy to install and preassembled off site, the amount of skilled labour needed on site to actually install is reduced, so low-skilled operatives with minimal training can be used during the installation process.
![]() |
What are the current issues facing modular installations?
Lack of early planning by the industry to accommodate a pluggable system at the design stage is one of the biggest things we see that needs to be addressed. We are actively working with specifiers and their customers to ensure they understand what modular wiring offers and why planning for its inclusion should be considered from the outset if the benefits are to be fully realised.
How will modular systems develop over the next five to 10 years?
We are very excited about the future. The cost- and time-saving benefits of modular wiring systems are becoming increasingly recognised, enabling electrical contractors to complete even the most complex installations more quickly and more efficiently than ever before. We will see modular wiring become more and more the norm, with less input required by product suppliers as the contractor becomes increasingly familiar with the concept and systems.
Dave Lewis is managing director of Apex Wiring Solutions