Looking to the future of BMSs
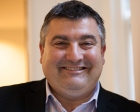
BMS has always been about using technology to enhance building operations. As the use of technology expands massively, has BMS had its day or is it now more vital than ever? Nick Clark of Point Building Controls looks at the future of BMS and explains how to deliver engineering best value by incorporating a Soft Landings approach.
When I first started in the industry there was very much a separation between the commissioning and service engineer. There were no out-of-the-box solutions, and we worked with the end client rather than an FM company. Though today technology has moved forward, the communication and understanding around BMS are still quite limited.
There used to be two different types of BMS engineer — commission, and service and maintenance. Now, we expect engineers to be technically proficient and multi-skilled enough to do both. A BMS can do so much more but, the more intelligent it becomes, the further away we seem to be from using it to its full potential.
In the past, I think, BMS fulfilled two main functions. One was to evaluate what you had and let you see where energy savings could be made. The other was to pre-empt the need to replace plant in the future. Unfortunately, in my experience, maintenance teams have tended simply to react to problems. This means they’re only using a fraction of what a BMS system can do.
Originally, BMS was called BeMS (Building Energy Management System), and I still firmly believe that building management systems should be used to create more buildings that use energy more efficiently.
Is the path for Soft Landings too bumpy to try?
Soft Landings is very much about creating better communication between all parties. By 2016, all central-government projects will be required to be based on Soft Landings and BIM (building information modelling). This requirement is driving larger companies to look at Soft Landings and to begin its implementation.
The ultimate aim of Soft Landings is to provide a smooth transition post practical completion and therefore give clients better value. When we operate a building the way it was designed to be, we reduce the likelihood of things going wrong, and we contain its operational energy. This benefits owners and tenants alike as they get to experience a trouble-free and efficient environment.
Unfortunately there is often conflict between contractors and clients. Applying low- and zero-carbon technologies often seems an afterthought and frequently goes unmentioned in the employer’s requirements.
Ashley Bateson, who chaired the recent conference on ‘Contemporary and soft landings for hard service providers’, commented: ‘Sustainability gets sacrificed in the recession. People who make capital cost decisions don’t normally have to live or work in the building that they are procuring and they may not be incentivised enough to think about end users.’
![]() |
Operating a building the way it was designed to be reduces the likelihood of things going wrong and contains its operational energy. |
He then went on to give a good example of where a forward planning approach such as Soft Landings can not only save both the client and end users time and money but can also achieve a better-controlled environment: ‘Project managers on a project agreed to cut out sub-meters in the school at the construction stage, as a cost saving. The contractors felt they did their job well if it was on capital budget; they were not encouraged, nor were the designers, to have a conversation with the end user about the removal of the sub-meters, which resulted in the client then retrofitting meters after the project was handed over — at a higher price than the original cost saving. It should be about more forward thinking and making the client aware that, if they can invest in energy saving and monitoring measures now, they could save twice the amount of money later on.’
Our own experience with using Soft Landings is that the commissioning process is much smoother. The manufacturer, client and contractor are all involved so they understand what type of system is being installed and essentially what they are getting for their money.
Metering and monitoring and monitoring again
A BeMS is ultimately a client investment. However, it’s often metering points which are the first thing cut to save costs. Ironically, it is precisely this data which can help the client save money in the years to come.
As a BeMS fanatic, I believe in monitoring everything — from alarms to alerts and including the environment. Maintenance teams don’t use metering tools enough; metering can cut energy use and help plant run more efficiently. Technicians must become more confident and knowledgeable in reading the data and making plant-related decisions.
Mind the knowledge gap
There is a big knowledge gap in the industry. Rather than just following PPMs, maintenance teams need to think more about proactive maintenance. When it is necessary to react to an issue, the maintenance teams in place need to be more confident about making necessary changes. For example, in the past, we’ve been called out for a ‘faulty BeMS’ which turned out to be just a blown fuse.
![]() |
The client vision of the scheme is quite often a Bentley while the contractor, due to financial constraints, wants a Ford. Clients may have limited knowledge, so the specification, depending on who is responsible for design, is more often than not over- or under-engineered. The client needs think of their BeMS as an investment rather than simply as a cost to be minimised.
The future of BeMS
In the last two years there has been a sudden surge of low-carbon technologies, many of which are wireless. This increase in technology means that these devices can be integrated into wireless BeMS. For example, maintenance task software can now be linked to the BeMS, so why not monitor the amps rather than do a bulk lamp change?
There are now many different BeMS packages on the market which enable you to incorporate wireless technology. Schneider has launched a web-based, dual-function BeMS, it allows different service to ‘talk’ to one another and other — external — services to be incorporated.
As a result, not only can we look at historical data but we can also start to use outside information, such as weather web sites, to predict the future. It’s such forward thinking that will enhance building operations and give a stronger role to the facility manager.
The facility manager, therefore, no longer has to simply follow the standard planned preventive maintenance programme; he or she can now be smarter about both reactive and planned maintenance. With BeMS technicians sitting alongside the contractor rather than underneath them, technicians can advise on the improvements that will provide the best-value engineering for a building.
There are now many small wireless devices which are simpler, much more powerful, and cheaper as they provide ‘no-wires no-batteries’ solutions. The big advantage of this to a retrofit client is that no trunking or cabling is required. This type of technology can now benefit smaller buildings where previously it was assumed that the cost of BeMS outweighed the benefits.
Apps can now be designed to work with the BeMS to provide live information. Nowadays, clients have full oversight of all the latest information, and FMs have the ability to adjust the BeMS and their plant machinery.
Take, for example, the recent St Jude storm at the end of October 2013. If you know in advance that a building is likely to be shut down for the day, you can make the correct preparations. Conversely, in the case of last year’s heat wave, it would have been possible — using the app — to turn the chillers on earlier and reduce the number of tenants complaining about being too hot or too cold. I know of instances where someone has been able to make adjustments halfway across the world, literally at the touch of a button.
So has the BeMS had its day? I think it has only just begun.
Nick Clark is sales director at Point Building Controls.