Energy as a lifetime issue
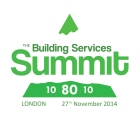
Services and the energy they use are a major contributor to the lifetime costs of a building. Ken Sharpe reports on a ‘summit’ that explored how to service buildings more effectively and with less energy.
The sequence of numbers 10-80-10 gives a succinct picture of the lifetime costs of a building. The first 10% is invested at construction stage. The 80% represents the operation of the building, The remaining 10% is represented by dismantling and demolition. So 90% of a building’s lifetime costs are entirely influenced by its design, construction and operation — which was the topic of the recent Building Services Summit organised by the Building Controls Industry Association and the services and facilities group of the Building & Engineering Services Association.
It was the acknowledgement of the importance of effective control systems in ensuring that building-services systems perform as they are meant to that brought the two organisations together. Malcolm Thomson, vice president of B&ES, summarised the philosophy: ‘If the controls aren’t right, there is no way the indoor environment can ever be right. It makes perfect sense, therefore, that B&ES members who design, install and maintain systems and equipment should develop a genuine understanding an appreciation of how their expertise dovetails with that of the controls specialist and how by working together each can enhance the other’s performance and add value to their contribution.’
Similarly, BCIA president Steve Harrison put the emphasis on controlling services such as heating, cooling, air movement, hot water and lighting. His focus was on firmly on saving energy.
Steve Harrison highlighted two main objectives of the summit.
• The long-term operational efficiency of buildings and how we can build this in from the start of a new project.
• How we can bring our existing building stock up to better standards of performance with controls.
![]() |
The long-term realities of operating buildings — Michael Dick, director of operations and buildings for the Barbican Centre and Guildhall school of Music & Drama. |
But even with the best of intentions, design plans can be rendered out of date by changing technologies, as Michael Dick, director of operations and buildings for the Barbican Centre and Guildhall school of Music & Drama, explained.
Work on this multi-use iconic building started in the late 1950s, and the last building was fully commissioned in 1982. Heating was originally intended to be provided by using what was then expected to very cheap nuclear electricity to heat water in huge storage vessels in a plant room below the Concert Hall. ‘Electricity was going to be so cheap that you wouldn’t even have to meter it,’ was the expectation of the age.
However, as Michael Dick explained, the system quickly became very expensive to run because of rising energy prices.
He described the scheme as ‘technically beautiful — with no flues, no mess, no fuss and very easy to control.
The scheme is now redundant, and has been replaced by hooking up to a local district-heating scheme that includes CHP. ‘At a stroke,’ said Michael Dick, ‘We met our carbon targets by moving over to district heating.’ All the tanks bar one are still in place because it is so expensive to remove them.
He also had an example of the over-enthusiastic use of a new building-management system to save energy. It was in the Milton Court concert-hall building and was used by the engineers to keep close control of services and their energy use. When the building was not in use for a period, the heating was turned off. However, when the heating was turned on again it was found that a lot of Steinway pianos had to be retuned — at a total cost of £40 000.
Inevitably BIM (Building Information Modelling) was a prominent topic in the day — and with good reason, for it addresses cost issues at construction stage, operational life and, ultimately, the end of a building’s life.
![]() |
In full Movember splendour, David Frise of the Building & Engineering Services Association discusses issues surrounding Building Information Modelling. |
The objectives set by the Government for BIM as summarised by David Frise, head of sustainability at B&ES, are ambitious indeed. They include 33% lower cost of construction, projects delivered in half the time and 50% lower emissions. And all that by designing, constructing and operating buildings more efficiently — not by sacrificing standards and misapplied ‘value engineering’.
With a wry tone in his voice, David Frise said, ‘BIM is the thing that is going to save the industry, for sure — because it is technology based.’
However, his concern is that the way the industry operates at the moment is not conducive to the effective take-up of BIM.
One of his concerns was that pressure to start work on site leads to a build-and-design approach [the opposite of design and build]. ‘We are an activity-based industry — that it, activity on site — and keen to get on site quickly, even if the project then takes longer to finish.
‘Design is not considered an activity. Planning is certainly not considered an activity. And these views drive up the costs of everyone in the supply chain.’ All of which means site start is not properly planned and prepared for.
David Frise observed, ‘Lack of forward planning leads to build and design. How do you design services if you don’t know what building they are going into?’
He warned, ‘If we try to introduce BIM into the way we currently do business, it will fail because is in effect just a technical cost.’
The secret of BIM is the data, rather than 3D CAD, and this is were the savings will come. His advice was that everyone using a common process for dealing with data, including product data templates, will lead to savings because work is not being repeated over and over again.
David Frise also had a suggestion for ensuring an adequate design before work starts on site. ‘The planning department could say that even with planning permission, you cannot start on site until you have a viable design, which someone will audit.’
While the importance of commission to the successful outcome of a project is generally acknowledged, the time available for commissioning and its quality of delivery are often compromised due to time pressures. As well as dealing with how the commissioning process should be prominent during the entire process, starting with pre-design, Glenn Hawkins of Clear Construction for the Commissioning Specialists’ Association highlighted some significant benefits of successful commissioning.
![]() |
The proven value of commissioning — Glenn Hawkins. |
One was energy savings, as revealed by a detailed study of 650 buildings in the USA. The study showed that the quarter of the buildings that were properly commissioned achieved energy savings of over 30%. Setting those savings against the cost of commissioning showed the payback period of commissioning to be less than a year — from energy savings alone.
Glenn Hawkins commented, ‘The other really good thing that I like about this detailed study was that it concluded something very simple — that the more thorough the commissioning process, the greater the savings that are produced.’
He also drew attention to the findings of another study of the costs that can be avoided through operational-readiness issues — such as up to 30% of a capital works project being destroyed. He observed, ‘The study also concluded that a properly executed commissioning process is the key success criterion to avoiding operational-readiness issues.’
Although many problems do not manifest themselves until late in a project, Glenn Hawkins is adamant that the key to avoiding them is recognising that the commissioning process should start at the predesign stage of a project with the formation of a commissioning team and producing a commissioning plan that defines how the commissioning process will be managed.
Major retailers and property companies in the UK have established a reputation for large-scale energy-efficiency measures. Sainsbury’s is one, and Phil Osborn, head of energy, gave an insight into the success of the company’s 20x20 sustainability plan for operational carbon, water and waste.
The target is to reduce carbon emissions by 30% absolute and 65% relative compared with 2005, even though the sales area has increased by over 45% since 2005. The plan is currently level with 2005, so there is still 30% to be achieved in just over five years.
![]() |
Driving down carbon emissions and energy consumption — Phil Osborn, head of energy with Sainsbury’s. |
The reason that Sainsbury’s is into energy and carbon management is that it is good for the bottom line. Phil Osborn said, ‘We do not do anything that does not make use money, and we have to compete for the investment that is needed.’
The approach has been to identify a number of energy-saving measures and select the most appropriate for a particular store to achieve the maximum energy savings.
The 20x20 plan is the successor to another scheme that ran up to 2012 and which achieved a 31% reduction in carbon-dioxide emissions per square metre compared with a 2005/06 baseline. The target was 25%. Energy-efficiency measure in existing stores contributed to the success, but a major contribution came from new stores, which are so much more energy efficient.
An example is the success of a ground-source-heat-pump installation at Crayford in 2010 leading to GSHP being rolled into the standard specification and now installed in about 20 stores.
With electricity being a major cost area for Sainsbury, a 12.7% reduction in electricity consumption since 2002/8 at the same time as store space increased by 40% is a significant achievement. New stores are clearly more efficient in their use of electricity, but existing stores saw a 24.1% reduction in electricity consumption. The cost saving is around £18 million a year at today’s prices.
LED lighting is playing a key role in reducing electricity consumption. In just two years 70 000 fittings have ben installed, many retrofitted overnight. and are delivering a saving of about 40% in lighting energy, or 40 GWh a year.
The energy efficiency of new stores is improving steadily as initiatives that have worked in a new store are rolled into a standard specification for future new stores.
Convenience stores of 200 to 300 m2 have also seen their energy consumption reduced, with an overage of 14% across 250 stores.
Renewable energy now accounts for about 15% of Sainsbury’s electricity consumption, a proportion that Phil Osborn comments could well increase as electricity use is further driven down.
CHP using green gas or biodiesel has been installed in nine stores and has a total output of 2 MW.
Much more significant than CHP is 135 500 solar PV panels with a peak output of 32 MW.
The latest initiative is for gas from an anaerobic digestion plant near the store at Cannock being piped to the store and generating all the electricity requirement. All the store’s food waste goes to the anaerobic digester.
Another Building Services Summit is planned for next year. We will let you have more details of the event when they become available.