Saving our energy future
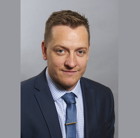
Replacing inefficient boilers, adding effective control and ensuring regular maintenance can transform the energy performance and comfort of a building, while protecting national energy security. Chris Meir examines at the role of condensing boilers in helping improve energy efficiency.
The building services industry has long recognised the importance of energy efficiency in achieving well performing buildings. And as energy security rises up the political agenda amid Brexit discussions, geopolitical tensions and reports of gas shortages, the focus on improving UK energy efficiency has intensified.
Certainly, addressing energy efficiency should be a priority for all organisations and businesses given its pivotal role in reducing energy usage, lowering running costs and cutting greenhouse gas emissions.
But where to start? New buildings are designed to use less energy – it’s the UK’s high proportion of energy inefficient commercial building stock that presents the greater challenge. Heating is typically the largest user of energy in a building, responsible for around half the total energy use. As such, it offers huge potential for significant efficiency gains.
A high proportion of non-domestic buildings use commercial boiler plant for their heating. The problem is that far too many still rely on old or inefficient boilers.
Which brings us to the role of the condensing boiler in improving energy efficiency. Replacing ageing boiler plant with affordable, high efficiency condensing boilers is a costeffective quick win for energy savings.
![]() |
Today’s boilers offer lower energy use and better performance |
Why? Firstly, condensing boilers offer the highest efficiencies of all boiler types. The latest models are capable of achieving near maximum efficiencies, reducing energy waste and so lowering costs. In contrast, a 25-year-old noncondensing boiler will operate at around 70% efficiency at best, even if well maintained, creating unnecessarily high fuel bills. That’s 30% of the gas input simply wasted.
Then there’s the environmental impact, as condensing boilers perform significantly better than non-condensing boilers in terms of greenhouse gas emissions. The latest condensing boilers typically achieve ultra-low Class 6 NOx emissions at or below 40mg/kWh while older non-condensing boilers are many times higher. Analysis by Aether and Amec put the figure at between 150-260mg/kWh . As such, the cleaner operating condensing boilers make a considerable contribution to the drive for improved air quality.
And by using gas effectively, condensing boilers make efficient use of national resources, helping support improved UK energy security in today’s politically and economically uncertain times.
48% gas savings
So what level of savings can you expect from an upgrade from non-condensing to condensing boilers? The European Union predicts a 20% reduction in energy consumption and emissions when replacing older equipment with products (like condensing boilers) that comply with the tighter efficiency requirements of the Energyrelated Products Directive (ErP).
The exact savings will depend on the nature of the boilers in place as well as the new heating system design. But a good example is Ferndown First School in Dorset, which has nearly halved gas usage since refurbishing its heating system with condensing boilers. By replacing the school’s old boilers with Remeha Gas 220 Ace condensing boilers and adding new controls, Dorset County Council has achieved a 48% drop in gas consumption.
This is just one of many examples illustrating the considerable benefits of a boiler upgrade. Aberystwyth University achieved a similar result when it refurbished the plantroom serving its William Davies research centre. Since replacing the ageing non-condensing boilers with Remeha Gas 310/610 Eco Pro condensing boilers and adding a new building management system, gas usage has fallen by 46%.
Zurich Insurance Services have also slashed gas usage at their Swindon offices. Initial indications are that replacing old, non-condensing boilers with Remeha Gas 220 Ace condensing boilers have resulted in 40% gas savings.
The common factor in all three projects is that the system has been designed to maximise the performance of the condensing boilers.
Condensing boilers operate more efficiently at part load as well as at lower return temperatures. Sharing the heat load across multiple boilers, as in these three applications, rather than selecting one single large output unit, allows the boilers to achieve optimum performance.
Thanks to their reduced footprint, condensing boilers lend themselves to multiple boiler installations. This configuration also improves the turndown ratio, enabling the boilers to match fluctuating heat demand more accurately, increasing fuel efficiency and extending the life of boilers by preventing on/off cycling.
At the same time, it provides designers and contractors with more flexible design options, thereby achieving maximum efficiency in a more compact solution.
And as condensing boilers up to 300kW can be installed on pre-assembled cascade systems and even bespokedesigned prefabricated rig units, installation is even faster and easier.
Given that 80% of the lifetime costs of a building are operational, we recommend adopting a routine maintenance and servicing programme to ensure continued high performance. Here again condensing boilers bring advantages as they are designed to enable simple part replacement and with an interior light for easier servicing.
![]() |
We should consider energy a resource to be saved |
Achieving and maintaining optimum boiler performance requires good control. Adding a weather compensated control helps the boilers adapt to the fluctuating demand according to the outside temperature to ensure still greater savings. In addition to time, optimisation and full temperature control, adding a sequential control to a cascade arrangement will rotate the lead boiler and lengthen the serviceable life of the boilers. Control settings should be checked on a regular basis.
Water condition can affect the performance and the lifecycle of heating equipment. It’s worth considering integrating a plate heat exchanger when installing new condensing boilers onto old systems to protect the new appliances from debris and contamination. Air and dirt separators will also help achieve and maintain good water condition on the primary circuit. The water should be routinely assessed to ensure good quality.
Implementing a planned boiler replacement programme is also advisable. The inbuilt redundancy of a multiple boiler design means that replacement, just like servicing and maintenance, is straightforward and can be carried out with no disruption to the heating provision. .
The financial and environmental arguments for replacing inefficient boilers are clear - lower operational costs, a reduced carbon footprint, cleaner air, and greater comfort levels for improved productivity. Now factor in their contribution to improved energy security, and well-controlled, well-maintained condensing boilers really do tick all the energy boxes.
Chris Meir is sales director at Remeha