Warm front
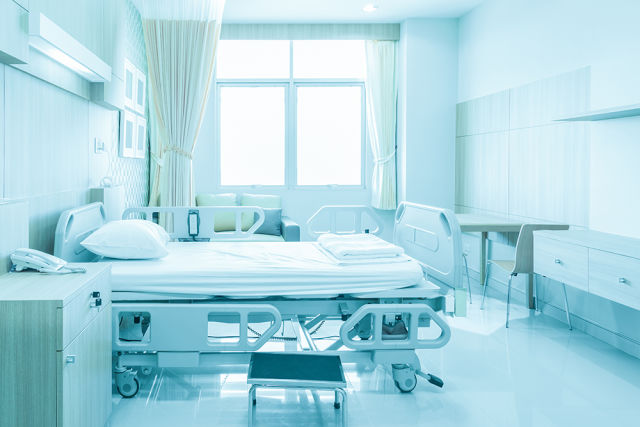
The NHS spends huge amounts of money on energy each year. Daniel Sturch examines an efficient and effective way to battle these costs and provide heating to these vital buildings.
Spending more than £750 million on energy each year, the NHS is one of the UK’s most energy intensive organisations. Modernising the energy infrastructure of the NHS estate is one way for our health service to spend less on energy and more on patients.
NHS Trusts looking to improve or replace their existing heating systems will find that the technology available to replace their existing appliances has changed significantly in recent years. This is why modern condensing cascade systems are seen as great way for hospitals to cut energy costs, increase reliability and improve environmental performance.
The Energy-related Products Directive (ErPD), introduced to the UK on 26th September 2015, established minimum energy performance standards for all energy-consuming products, including boilers, with outputs between 70kW and 400kW. The directive states that the useful efficiency of these boilers when operating at full capacity shall be no less than 86%, and at 30% load, the useful efficiency should be 94% or higher.
The non-condensing boiler technology typically installed in hospitals before this date is unable to meet these standards, and so has been phased out and replaced with condensing appliances instead. Now, NHS Trusts who are looking to upgrade their heating and lower their energy costs must consider installing a new system based on condensing boiler technology, rather than relying on the same technology they previously had.
For those commercial Gas Safe registered-installers being asked to upgrade or retrofit hospital heating systems, cascade boilers offer a practical solution to ensure they comply with the new regulations, while also providing the high efficiencies that their clients require.
A cascade heating system comprises a number of condensing boilers connected through hydraulic and gas pipework, linking each boiler and flue together. The engineer then uses modern controls to ensure they operate efficiently in sequence, providing peak load heat outputs when needed, and modulating down as much as possible when they are not required. Cascade boilers can be wall-hung or freestanding or supplied pre-fitted into purpose-built freestanding frames to make them faster and easier to install.
This is of particular importance for hospitals, as it means new boilers can be installed quickly. This is integral if they are unable to accept patients or are required to close certain wards while the heating system is being renovated. Considering the vital work hospitals carry-out for the community, anything that can be done to minimise disruption to patients and staff should be considered as a matter of urgency.
While each individual boiler offers a certain level of central heating output, when several boilers are sequenced to work together in cascade they can create a system with a total heat output that is far higher. Condensing boilers have outputs between 54.8kW and 121.7kW. However, when up to eight boilers are used in cascade, installers can create cascade systems of over 970kW – more than enough to supply sufficient heat for most good-sized hospitals.
The main benefit of specifying a new cascade system for a hospital comes from the step-change in efficiency it offers. Modern condensing cascade systems are significantly more efficient on initial installation, offering 96% efficiencies, compared with the lower efficiencies offered by older boilers that could have been as little as 50% to 60%. This means that even a like-for-like installation in terms of potential output would improve the hospital's overall efficiency substantially.
Installing like-for-like systems used to be a popular choice in retrofit situations, as the engineer could be reasonably sure that the system would provide sufficient warmth for the hospital, so long as the original installer had correctly calculated the system load and the occupants had not already been experiencing problems with insufficient heat.
However, the new requirements of the ErPD mean that, in many cases, like-for-like appliances will no longer be possible. Even if these appliances were still on the market, specifying a simple ‘like-for-like’ installation is no longer considered best practice, especially in a hospital that has been open for a long time, as it fails to take full advantage of just how efficient commercial condensing boilers can be when fitted in cascade.
There are two main reasons why engineers will need to do more than just swap out the boilers. Firstly, while modern condensing boilers are significantly more efficient than the boilers they are likely to be replacing, to take full advantage of that potential, the system must be designed so that the boilers operate in condensing mode for as long as possible. This may require wider changes to the system design that would not have been necessary when the original system was installed. Condensing boilers will only operate in condensing mode, and therefore at peak efficiency, when the return temperature of the water (also known as the Dew point) is 55°C or lower.
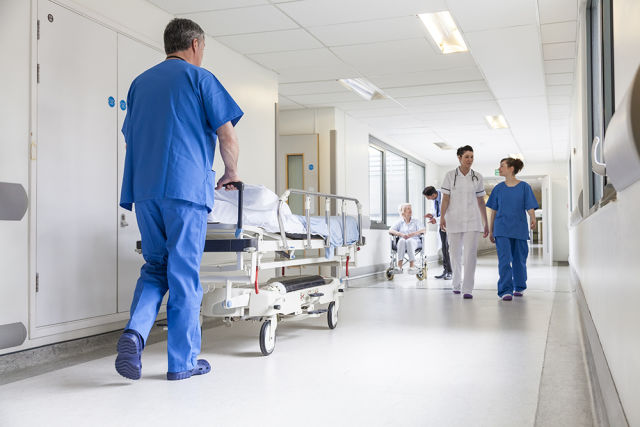
Installers should find out when the building’s energy usage is likely to be at its highest, and under what circumstances, to best calculate its peak heat demand during the coldest time of the year. This may require them to spend time with the NHS Trust and facilities or building maintenance department to work out exactly when the system is most likely to need to operate at full capacity. Is it during weekends when the Accident & Emergency Department is likely to be at its busiest? Or does this hospital specialise in planned, routine operations? In which case, weekdays during office hours are likely to be busier. How does the heating system need to react to changes in occupancy patterns?
Then, the installer must assess how much heat is lost through the fabric of the building, and factor that into their system design. The system must be able to satisfy the building's peak heat demand at the coldest time of the year, while still being able to modulate down to lower temperatures and operate more efficiently when that heat demand is reduced.
For example, a condensing boiler with a modulation range of 1:10 means the maximum possible output of 55kW can be reduced to just 5.5kW if there is a lower system demand. For a cascade installation of five such boilers working together, the modulation range improves five-fold, resulting in a possible modulation of 50:1.
This high modulation ratio means the boilers can be commissioned to operate at part-load for longer, matching the system demand far more closely at all times. This means each boiler is less taxed, reducing the wear and tear on the components.
For example, a heat load requirement of 90kW could be satisfied using a cascade system of four 50kW boilers, each modulated down to operate at 22.5kW. With each boiler running at part-load, fuel efficiency rates would be high. Alternatively, if the hospital does not have the budget to install four boilers at once, a two-boiler cascade system could be fitted instead, with one 70kW model operating at full load, and the second boiler modulated down to 20kW.
A cascade system can only provide heat that closely matches the changing heat load using the correct controls, to ensure they modulate together to match the load and keep the boilers in condensing mode for as long as possible.
With a carefully designed system of controls to monitor the energy demand and ensure that the design temperature differential between the flow and return water temperatures is maintained, the cascade boilers will accurately respond to the exact heat demand placed on them by the occupants, delivering impressive efficiencies at all times.
Purchasing a cascade system from one manufacturer means the installer can be confident that all the components and controls will work together seamlessly, rather than trying to build a system themselves from disparate products that are not designed to work together.
For NHS Trusts looking for ways to improve their efficiency, lower overheads and increase profits, upgrading their heating to a cascade boiler system offers a great opportunity to make significant savings in the long term, while also enjoying the reassurance that their heating system will be reliable for years to come.
Daniel Sturch is from Alpha Heating Innovation