In the pipeline

Using one pipe connection method across a project can significantly impact the speed and success of an install. Scott James highlights the benefits of modern approach to pipework for building owners and installers.
Taking a large commercial building as an example, it is entirely possible that there will be a mix of copper pipework for the hot and cold water systems in kitchens and washrooms and thick-walled steel tube for the heating distribution system. In this case the installation teams will require the equipment to both solder the copper and to add a thread, cut a groove or weld the tube.
As a result, it could be assumed that there is no single pipe connection method that can be used without a degree of compromise but there is an alternative. Today’s press connections can provide the versatility needed for a whole project. Products suitable for a wide range of applications are available including heating and chilled water, potable water, natural gas and LPG, technical gases and fire suppression systems.
Where used throughout a project, the press connection approach also offers a solution for linking different types of pipe materials. They can be used on metals such as copper, stainless steel and carbon steel as well as plastic multi-layer pipe in a variety of sizes, and at a range of temperatures and pressures. Adapter components are available that not only allow both sides of the connection to be pressed but also integrate with threaded pipe if required. Although the specific product used for each application and material will vary, the installation process is identical.
Similarly, public sector projects until very recently only used welding, grooving or threading as a connection method for the thick-walled steel tube which is often required for these projects to meet increased durability requirements. However, innovations in press connection technology now allow tube up to four inches in diameter to be connected, delivering up to 80% time saving when compared with welding.
Other benefits of standardising the installation approach across the whole project are clear too. Take training for example. Because the installation team only has to be trained on one type of system, the training process is streamlined considerably and for teams that are using press connections for the first time, many leading manufacturers offer on-site training.
It also means the team is able to work more flexibly and consequently more efficiently. This is particularly valuable on-site when the construction schedule requires a section to be completed to a fixed deadline. The contracts’ manager can transfer personnel working on another area easily, confident in the knowledge that they are familiar with the products.
The simplicity of the press connection system means that it is easy to train operatives on the products and equipment at the start of a project. To create a robust joint using a press connection, installers just cut the pipe to size, deburr the cut surface, slide the fitting onto the pipe and press the connection. The press tool will apply the correct level of pressure and will release when the joint is complete.
Similarly simplified is the mobility of the equipment. Due to the size of the machinery required traditionally to create a thread or cut a groove, it is often located a distance from the point of installation. In contrast, when using modern press connections, the press gun and tools can be easily carried by each operative and located where required.
This method also allows installation times to be reduced significantly, removing the need to prepare the pipe surface before and clean it after as with soldering. While time savings will vary depending on the pipe material and the alternative connection method, a reduction of between 30% and 80% per joint can be achieved easily. For example, compared to welding or threading, press connections can achieve up to 60% reduction in installation time for sizes up to two inches and as much as 80% for the larger diameter tube.
The fact that this method does not require skills such as welding or soldering not only addresses the challenge of the skills shortage being experienced but also means that the quality of the joint is consistent too and is not dependent on the abilities of the installer.
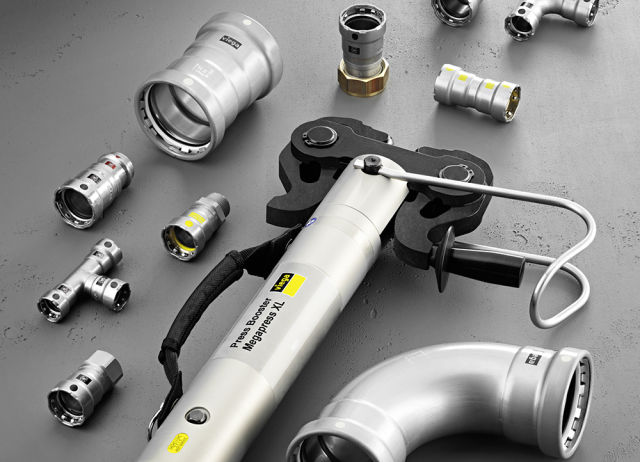
Despite soldering and welding being considered the go-to method for decades, press systems can create a stronger, more reliable joint. Products that feature a double pressing – before and after the compression will create a permanent seal that resists both torsional and longitudinal forces.
The benefits can also be seen when it comes to leakage testing of the system. The nature of the press connection method means that the joint is either fully pressed and secured or missed entirely. If this is the case and a leak is discovered, the missed fitting can be pressed immediately without the need to drain the section or dry the area around the joint.
Nevertheless, it is crucial to select a system that ensures the fitting will leak when tested if unpressed. Poorly designed products may hold during testing only to begin leaking when the building is complete and occupied – resulting in the need for costly remedial work. In contrast for example, the SC-Contur technology built into Viega fittings guarantees a visible escape of water from the connection when the system is filled for the first time. It also allows dry testing with an inert gas, where a measurable drop in pressure will occur if a connection has been missed.
A final point to add concerns the health and safety benefits of adopting this approach to pipework. According to the Health and Safety Executive, the UK construction sector tends to come out as one of the worst in terms of the greatest number of fatalities each year, so any way of improve health and safety on-site is worthy of consideration.
As a cold-applied system, press connections avoid the need for hot works and as such can be used in any area of a building. This overcomes the issues faced when installing pipework in areas with a higher risk of fire or combustion. Additionally, a recent Health & Safety Executive (HSE) Bulletin reclassified mild steel welding fume as a human carcinogen. As such the HSE is enforcing stricter regulations when it comes to welding which will include more equipment, further training and monitoring – all of which increases time, labour and costs.
Ensuring that each stage of a build is completed as efficiently as possible is what builds reputations. So, for plumbing and heating contractors looking to avoid time delays and costly remedial work, choosing the right pipe, connectors and fittings for a smooth and successful installation has never been more important.
Simplifying the installation process across a project using a single connection method offers significant benefits for not only the M&E teams but for the overall construction programme too. With the range of materials and applications for which press connection technology is suitable, it delivers greater design and on-site flexibility, simpler training requirements and reduces the equipment needed on site. These benefits, coupled with improved safety and reliability, all contribute to the speed and success of the install as well as the longevity of the system. It is a win-win for all involved.
Scott James is director at Viega