Unsung heroes
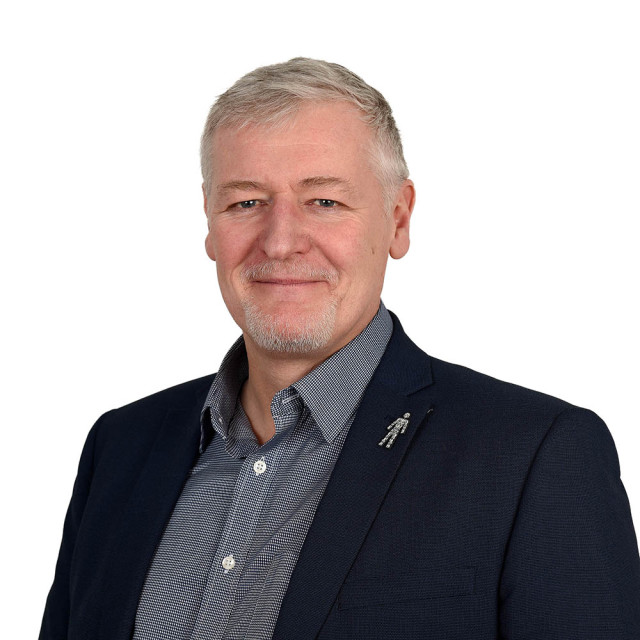
Expansion vessels are an essential element in any commercial heating system but ensuring you have the right one requires complicated calculations. Here, Rob Jacques discusses the complexities of this ‘simple’ technology and offers guidance on making the right choice.
As every secondary school science student knows, when hot water is heated it expands. In a closed heating system the ‘excess’ needs to go somewhere. That place is an expansion vessel.
But it’s more than just a temporary holding space. Without it, the pressure would build with potentially disastrous consequences, not least the safety valve lifting. Then as the heated water cools the vessel replaces it back into the system, helping maintain a healthy working pressure, keeping within maximum and minimum boundaries.
![]() |
Yet while the science is straightforward, its application and the subsequent installation are less so. And the place where it often goes wrong is in the specification. Before we come to how you select the right vessel for your system, let’s recap on what it is, what are a vessel’s component parts.
Simply put, it’s a steel container with either a diaphragm or a bag inside. On one side of the diaphragm (or within the interior of the bag) is the system water. On the other side of the diaphragm (beyond the bag’s exterior) is air. It’s at this point that the questions begin. Do you go for a vessel with a diaphragm/membrane or one with a bag?
The material can be EPDM (Ethylene Propylene Diene Monomer) or butyl; both are synthetic rubbers. Bags need to stretch less than diaphragms and tend to be made from butyl, but they are more expensive. Diaphragms must be EPDM as they have more stretching to do.
However, EPDM is more porous to air than butyl and, therefore, it loses pressure more quickly. Also, because it has to stretch more than a bag the diaphragm is more likely to fail, particularly where it connects to the container.
Of course, the other ‘component’ in the vessel is the air (or nitrogen) with which it is pre-charged. This pre-charged air maintains pressure on the outside of the bag or diaphragm, acting as an ‘air cushion’ and thereby controlling how much either can stretch.
BSRIA and CIBSE recommend that the vessel pre-charge pressure is checked annually for any loss, although this may be too long a period if you find yourself with a poorer-quality vessel.
This pressure loss can vary from 3% to a hefty 48% in a year; losses of just 15% will begin to affect pressure control and, if unchecked, problems can start from four months after start-up. For the expansion vessel to operate correctly, the vessel pre-charge pressure must be adjusted specifically for the site conditions.
In a commercial set up, where the heating system is servicing a large building, the vessel will be used in conjunction with a make-up unit, together forming a pressurisation unit. The make-up unit constantly monitors system pressure and adds refill water to maintain a minimum pressure, while also alerting the end-user if the pressure moves outside the design operating range.
Of the two, the vessel is the most important, but system specifications often do not reflect this, instead focusing on the make-up unit features. Failure in the make-up unit isn’t a good thing, but losing the vessel means a total loss of control of the system.
We’ve dealt with the basics of what comprises an expansion vessel. Let’s now look at some other key factors and terms. Vessel acceptance is the percentage volume that the vessel can be filled with water, while adhering to the maximum permissible according to the manufacturer’s instruction, the vessel’s relative location and the design parameters of the system (or limits to its operating range).
The vessel reserve is the minimum amount of water required in the vessel under all operating conditions. If there is no water in the vessel it does nothing and you have no pressure control. According to British Standard EN12828, vessel reserve is taken as 0.5% of system volume. This level of water is required to provide hydraulic back-pressure from the vessel thus stabilising system operating pressures, particularly with pumps.
Lift pressure relates to the safety valve on top of the vessel. There is a calculation required to determine the safety valve lift pressure (Psv) and, therefore, which one is correct. The ‘neutral point’ - is the position at which the expansion vessel is connected to the system and should always be on the inlet side of the pump. It is essential to locate this correctly to ensure all other pressures can be calculated accurately.
Expansion pipe sizing is the section of pipe that connects the vessel with the system. It must be sized to generate minimal frictional loss. Too narrow a pipe will lead to over-pressure during heating and under-pressure during cooling. This will give unnecessary alarms and unwanted water make-up (introducing fresh oxygen), making it prone to sludging up and blockage.
The pipe size is dictated by the rate of volume / temperature change of the liquid i.e. proportional to the kW output of the system. However, if the specifier does not stipulate the size on their drawing, the contractor will often do it as small as possible to minimise cost.
It’s worth remembering that imperfect installation does not have to be a major error to have a big impact on overall system performance.
![]() |
Determining the vessel size
When determining vessel size, a degree of concentration and a level of determination are needed. To determine the vessel size, and comply with regulations, we must know the following:
• The static height, measured from the top of the circuit to the centre line of the vessel
• kW output, which determines the expansion pipe size
• System volume, can be calculated or estimated from charts and/or kW output
• Maximum temperature, in order to select the correct expansion coefficient and to determine if intermediate vessels are required.
This leads to the calculation ‘Total expansion’ divided by ‘Acceptance’, as a result of which the next largest available vessel is the one that should be installed.
There are two British Standards that provide the relevant guidance for central heating systems. They are BS EN 12828, covering the design of water-based heating systems in buildings, and BS 7074, giving guidance on the correct specification for expansion vessels.
By adhering to both you arrive at the correct pressure range for the expansion vessel in relation to the size and demands of the building.
But with some installations the designer has stopped part way through BS 7074, which means the full calculation hasn’t been done. As a result the vessel is too small, the pressure is excessive, the membrane is stressed and you can end up with the safety valve lifting. That can lead to water loss, chemical pollution, the potential for air to be pulled into the system, leading on to poor flow, water starvation and a multitude of problems simply for not doing the full calculation.
Another issue is that designers often turn to online calculators, but their accuracy is questionable and none are verified externally. System designers must always take BS EN 12828 and BS 7074 into account, including the latest updates, and do the full calculation.
Rob Jacques is national key accounts and technical sales manager for Spirotech UK