Getting the package right

Demand for packaged plant and modular construction is continuing to grow. Here, Roger Hoskins of Conex Bänninger discusses the opportunities for the HVAC industry and offers some tips for achieving a successful offsite project specification.
Look at all of the different sectors and all the talk is about an increased focus on offsite, or modular, construction. School projects, hospital rebuilding and particularly new housing, all have recently received a nudge in this direction from the government in support of its ‘Construction 2025’ strategy. Whether it’s an order to use as much MMC (Modern Methods of Construction) on a build as possible or seed funding for an MMC taskforce, there’s no avoiding it’s a manufacturing and assembly methodology that is going to grow and grow. Just a few years ago M and E contractors would do the ‘traditional versus modular’ build calculation. Nowadays many go straight to modular.
For the HVAC sector, typical opportunities for growth for packaged plant are wide ranging. They include building services, for everything from offices, schools, and multi-occupancy residential schemes to prisons and hospitals; manufacturing, for heating, pump and OEM package manufacturers; and for industrial applications, such as process pipework, power generation, food and beverage and pharmaceutical. All will demand bespoke solutions that will require complex manufacturing processes beyond just plain pipe bending, for products such as skid frames, pipework systems and modular valve assemblies.
The advantages of packaged plant over on-site construction are well established. Faster speed, repeatability, improved health and safety, a controlled environment, and reductions in labour costs are some of the key ones.Also, advances in the systems and materials used mean, in many cases, that the adoption of packaged solutions enables a bigger contribution to be made towards sustainability objectives. In the HVAC industry, the introduction of new technologies and new product ranges have enhanced the opportunity to participate in this burgeoning sector. The development, for example, of the flame free press fitting system for completing pipework joints matches the requirement for greater speed, certainty and cost control.
Co-operation and communication
If the unprecedented events of the past 12 months have achieved anything positive, it is that it has accelerated digitalisation in the construction industry, including the HVAC sector. All along the supply chain ‘new’ forms of communication have been adopted and, in particular, a reliance on data-rich sources of information, such as BIM modelling (Building Information Modelling), have increased.
Be it a project consultant, specifier, building services engineer, or M and E contractor, there is now an expectation among them that this higher level of detail is made available by manufacturers. Those that don’t will miss out. Indeed, digital collaborative platforms such as NBS (National Building Specification), on which BIM objects can be accessed, are helping drive a change in culture that is leading to greater co-operation and sharing. The BIM objects, for example, that are available for all our >B< Press fittings ranges have been created in accordance with ISO 23386:2020, which means they are machine-readable, versatile and consistent across different software.
While making the above available is essential for a successful offsite project specification, it is only part of the story, a process in which I would summarise the key stages as ‘project review’, ‘design’, and ‘manufacture’.
Project Review
For the project review stage, early engagement with stakeholders is essential. By applying DFMA (Design for Manufacture and Assembly) principles, which focus on simpler manufacture and efficient assembly, this then drives the project design, with the building services built around the offsite solution.
This early engagement ensures that stakeholders are clear which MMC are to be used, benefiting the project hugely as all stakeholder contractors will have an understanding of, and can input into, the design process. Careful consideration should also be given to the product application and selection, looking at any potential limitations or restrictions. This will mean that any impact the offsite solution may have on building or other services will be known at an early stage. Every project brings a different set of challenges. Factors such as access, delivery, and health and safety, all must be taken into account.
The offsite manufacturing needs to overlay the main construction programme accurately, without early engagement the lead time may become an issue.
Design stage
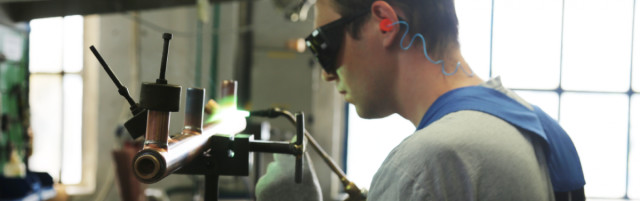
Putting a bespoke HVAC solution together is often complex, so having to continually alter the design because the building model is being changed can be extremely challenging. This can be partly overcome by ensuring the CAD Revit model is fixed, avoiding this distraction in the design process. Another pitfall to be avoided is a clash with other building services that would affect the offsite solution.
When your packaged solution, in the case of HVAC, can be found in anything from corridor pipework to rooftop assemblies, from plantrooms to building risers, there’s plenty of opportunity for accidental conflict if not managed properly. By carrying out ‘clash detection’ at this stage, often design features can be built into the offsite solution to mitigate this and assist with co-ordination.
Managing the build programme
For the manufacturing stage, when designing an offsite solution, it is always wise to be mindful of any component lead time, otherwise there may be delays caused by the availability of product that is part of the solution. Also, by utilising their project management skills and experience, offsite manufacturers will often be able to highlight any potential programme slippage early in the project and propose action. Setting up a factory assembly approach to manufacturing requires quantities to achieve economy; key to any offsite solution is standardisation and being able to produce to volume. So, building lots of different versions of the same thing is not practical and will only overcomplicate what should be a simple process.
Pressing ahead
As well as bespoke products, most solutions are likely to be coupled with ‘DNA’ products, which brings me back to the benefits of press fittings and the suitability of this technology to modular construction. Unlike with the slower, traditional brazing method, the time taken for each pressed joint is consistent. This predictability makes it easier for project managers to plan more effectively, with a subsequent cost-per-day reduction achievable for the main contractor.
Being flame-free, the risk from fire is eliminated and there is no need to go through the time-consuming process of applying for hot works permits. It is also friendlier to the environment as no hazardous gas bottles, or jointing materials such as solder, are required, the joint being completed with an electro-mechanical press tool and jaws set.
New skillset
Finally, while there is still a lot being said about skill shortages in the wider construction industry, the ease of use of press fittings has brought a new set of skills that are in tune with the requirements of offsite construction packaged plant. Implemented properly they ensure increased productivity and whether delivered on-site, as per pre-pandemic, or online through webinars, they can be quickly learned. Having completed the brief period of training, the heating engineer or installer has the necessary skills from day one.
Roger Hoskins is Project manager at Conex Bänninger