A word on... LEV testing
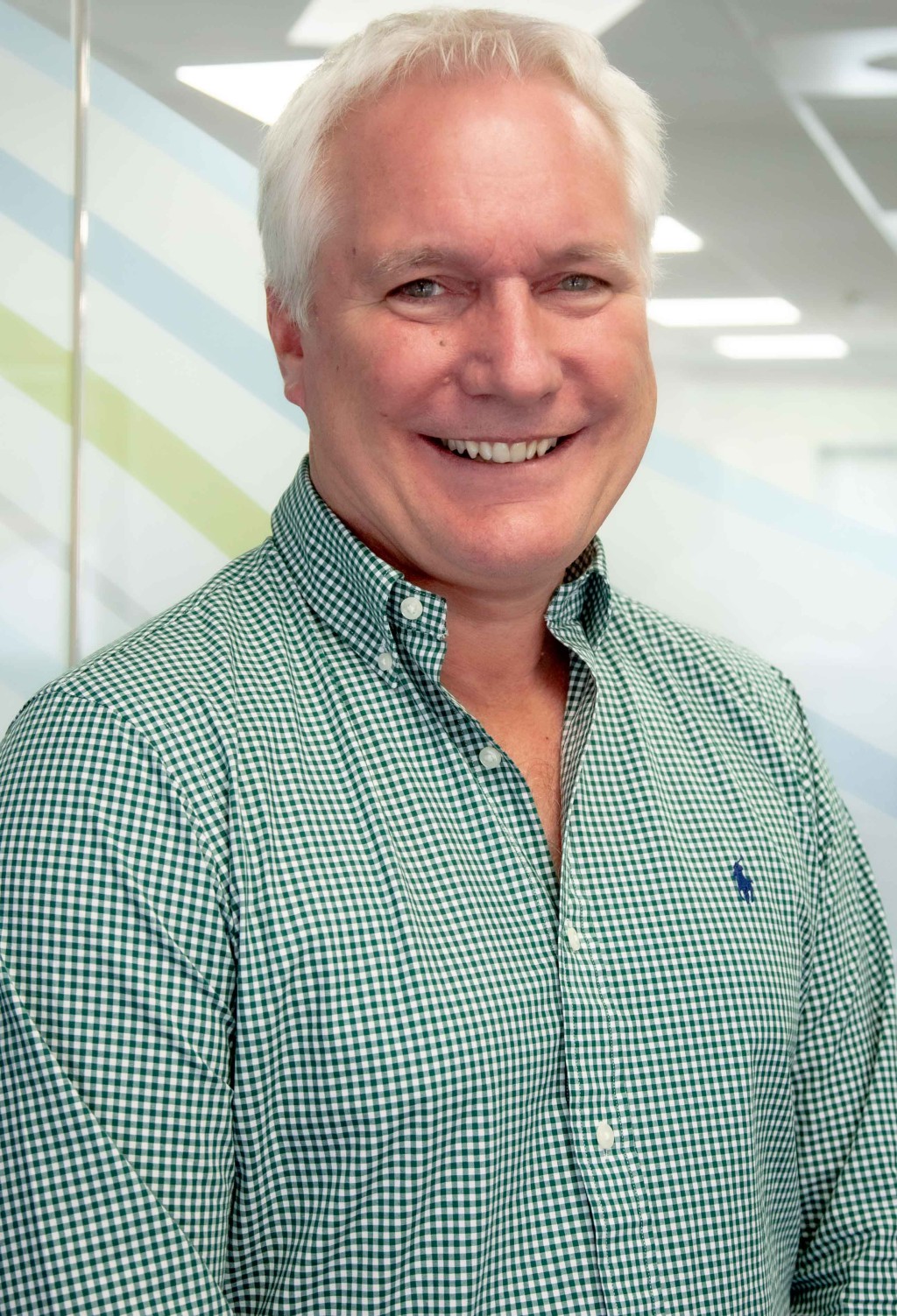
Andrew Steel, Managing Director at Airmec Essential Services, highlights the importance of accurate testing of local exhaust ventilation systems.
The Health and Safety Executive (HSE) has acted on its concerns about assessors passing sub-standard local exhaust ventilation (LEV) systems as fit for purpose and exposing hundreds of people to unacceptable – and unlawful – levels of risk. Action has been taken against employers who had failed to appoint a competent person to thoroughly examine and test their LEV plant, and the testing companies concerned have been served Improvement Notices and named and shamed on the HSE website.
It may come as a surprise that the employers were held to account for the inadequacy of contractors but, as we always warn about all of the essential services we offer, the buck stops with the person responsible for operating the building, be it the owner or occupier. Yet you have to rely on specialist engineers to advise you of faults and dangers, so it is vital to choose your service provider wisely and to challenge them to prove that they are competent.
You need to know that they understand the law and what qualifications and standards the individuals who work at your premises should have. If in any doubt, ask.
What is the law on LEV testing?
A workplace that uses any kind of process which creates harmful airborne contaminants including dust, oil mist, welding fumes, smoke and vapours will
require LEV that removes the contaminants from the air before they can be breathed in. Capture hoods are probably the probably most common form of LEV.
The law calls for regular LEV testing at least every 14 months by a competent person.
The Control of Substances Hazardous to Health (COSHH) regulations tell you what you
need to do. The HSE’s HSG258 ‘Controlling airborne contaminants at work: A guide to local exhaust ventilation (LEV)’ guides you on how to do so.
COSHH is the law that requires employers to control exposure to materials in the workplace that cause ill health.
You can prevent or reduce workers’ exposure to hazardous substances through:
• risk assessment
• control
• management
• maintenance
• training
• monitoring
• planning for emergencies
How to keep your LEV systems safe
HSG258 defines how LEV systems should be examined and tested by a competent person, at least every 14 months.
Testing involves thorough visual and structural examination and testing (often abbreviated as TExT). HSG258 says it must be done by a competent person and must include checking the airflow to make sure that the system is adequately removing contaminants from the air. You must keep proof that your LEV system has been tested and passed on file for a minimum of five years.
Who can test LEV systems?
What is competency in LEV TExT? The recognised qualifications are the British Occupational Hygiene Society’s (BOHS P601: Examination and Testing of LEV Systems). You also should expect your service provider to have that good knowledge of systems design which is certified by the P602: Basic Design Principles of local Exhaust Ventilation Systems qualification. At Airmec we regularly inspect and test LEVs in various locations and can advise on and undertake remedial works required.
What can go wrong with LEV?
Problems reported by the HSE include:
- the capture zone does not cover the whole working zone
- inadequate airflows (i.e. reduced or no detectable airflow)
- badly damaged ducting and hoods
- blocked ductwork
- damaged or missing filters
Of course, there is also the risk of bad practice and people not really appreciating the risks. ‘Clearing the air’, a simple guide to buying and using local exhaust ventilation, is free to download from the HSE website.