Flueing for biomass boilers
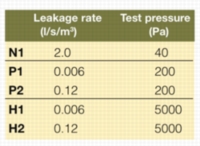
Jim Murray for the BFCMA* looks at the requirements and standards related to flues when using biomass as a fuel.
Biomass fuels, or biofuels, are, and will remain, an important part of UK Government’s renewable and sustainability agendas. Biomass itself is a renewable energy source derived from living, or recently living organisms, such as wood, waste, crops etc. Biomass is generally plant matter grown and harvested to produce heat or act as the prime mover for generating electricity. For example, biomass can be grown from a wide variety of plants and trees, which can then be re-planted, or obtained from waste such as dead trees, branches and tree stumps, yard clippings and wood chips. Not only are specially made boilers required to burn biofuels, but there are also special flue requirements. To help fully understand the requirements of flues for biomass fuels, an explanation of the new CE Designation Marking System is relevant. The standard for the construction and installation of flues and chimneys is BS EN 1856 - 1:2003 ‘Chimneys. Requirements for metal chimneys. System chimney products’ (introduced on 1 April 2005). This standard covers performance requirements for metal chimney systems such as twin-wall prefabricated chimney systems and liners. The diagram below explains exactly how a metal chimney system is designated. As can be seen from the designation, a complete specification of the chimney or flue’s operating scope can be ascertained. For example, the temperature rating is the maximum temperature (°C) for continuous use of the flue. T450, as in the example, is suitable for multi-fuel, and T200 would be suitable for gas and oil. The pressure rating is expressed as N for negative pressure, P for positive pressure and H for high positive-pressure applications. Maximum allowed leakage rates are as defined in the table. For most applications, N1, as used in the example, is suitable for conventional negative-pressure boiler installations. P1 is required for most positive-pressure and fan-flued boilers. H is for high-pressure applications such as diesel generators, when the leakage rate is normally subject to specifier requirement. The nomenclature for condensate resistance denotes whether the flue is suitable for wet or dry operation. W, in the example, designates ability to contain condensate within the flue, i.e. operating in the wet and dry conditions created by condensing appliances. D designates ability to operate under dry conditions only, usually meaning a flue-gas temperature high enough to avoid condensate formation. Corrosion resistance depends on the fuel type to be used and is designated as follows. V1 is tested and approved as resistant to attack from products of combustion from gas. V2 (as in the example) is tested and approved as resistant to attack from products of combustion from light oil (sulphur content up to 0.2%) and natural wood. V3 is tested and approved as resistant to attack from products of combustion from heavy oil (sulphur content >0.2%), solid fuels and peat. Vm is not tested and approved, but its rating is declared by the manufacturer. Two features are next specified — a code for the minimum material grade and the material thickness. Flue liners expected to withstand the corrosion effect of multi-fuels, wood or heavy oil are normally made with 316L stainless steel. Light oil is less corrosive, and normally 304 stainless steel has proved adequate in dry conditions; however, in the increasingly common wet conditions created by high efficiency boilers, the higher grade 316L is required. The next designation is expressed as either G (as in the example) with soot fire resistance, or O without soot fire resistance. This designation is followed by the declared minimum distance to combustibles expressed in mm. To obtain the G classification, the product has to be tested at 1000°C for 30 minutes and remain intact, and the temperature of combustible material at the designated distance must not exceed 100°C at an ambient temperature of 20°C. Products with O classification mean the product is not rated as soot fire resistant. Normally this will occur with low-temperature applications such as condensing gas boilers, where lip seals are used, which would not withstand a soot fire. This definition can be easily misunderstood, and it has to be read in conjunction with the soot fire resistance classification and is not a stand-alone parameter. The CE Designation Marking System is laid down as follows: G 50 or G 75 is the distance declared as the safe distance to combustible material. In relation to biomass fuels such as wood chips and pellets, the general opinion is that such fuels are capable of creating ash deposits within both the boiler and/or the flue system, thus creating the possibility of a soot fire. The new CE norms set out the criteria in which a chimney system subjected to such a soot fire condition would remain safe. The type of material and construction of the flue which are capable of surviving such conditions can only be assured by the use of flue systems with the G designation as described above and used with either W or D (wet or dry) for condensing or fully dry systems with a corrosion resistance class of V2 (wood) So, for biomass fuels a typical designation may read EN1856: T450 N1 W V2 L50 050 G 75 as in the example. It is important to select the correct flueing arrangement when designing for biomass, as the requirements are different to those for fossil fuels. The HVCA has a ‘Guide to good practice for the installation of biofuel heating’, TR/38, and offers information on the flueing requirements for ‘woody’ biomass as well as other aspects of this fuel. Biomass as a low/zero carbon fuel will have a key role to play in the UK’s future heating strategy and will greatly assist in achieving the renewable targets set by the Government. It is important to note that within smoke-control areas biomass in the form of logs, chips and pellets can play an important part in the heating strategy, but must only be used on exempt clean-burn appliances that have been specifically tested and approved under the Clean Air Act. *British Flue & Chimney Manufacturers’ Association’
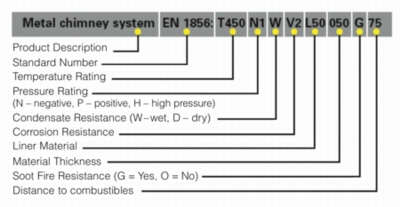