Small but smart
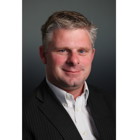
Stephen Hart explains that while small flow paths in two port control valves can be unavoidable, the risks can be mitigated by smart system design and product selection.
Energy efficient pumped hydronic systems generate heated or chilled water in a central plant room or energy centre before it is distributed through a piped secondary system by variable speed pumps to each terminal unit where water flow is throttled by two port control valves to regulate the heat transfer to or from the space air to maintain the indoor climate at a comfortable temperature (see Figure 1).
System devices such as heat exchangers, regulating and control valves, sensors and probes are generally selected and sized to deliver good climate control rather than resilience to dirt or ease of flushing or commissioning. Unfortunately, the performance of these devices can be significantly impaired by poor water quality and great care should be taken to avoid introducing dirty system water into terminal circuits containing these devices.
![]() |
Figure 1: A typical variable flow secondary circuit |
![]() |
Figure 2: Pressure indepedent variable temperature injection circuit |
Whilst strainers can be installed in branch or terminal circuits to filter out debris from system water these will often be bypassed during elements of the flushing process, leaving devices and control valves exposed to debris such as pipe joint compound and other materials left from the pipework installation process
Passive heating and cooling terminal units can be selected with relatively large bore control valves for on/off control, but it is necessary to select two port control valves with much smaller flow paths in order to achieve high authority for good modulating control of active heating and cooling terminal units such as fan coils and active chilled beams. Modern, well insulated buildings and the trend towards high delta T’s to maximise the efficiency of heat generators such as condensing boilers have contributed to the reduction of design flows through terminal devices.
Furthermore, as small two port control valves must exert authority over higher differential pressures than similar sized four port valves they will generally have much lower Kvs values and smaller flow paths when sized correctly for good modulating control. Typically, PICV’s will have higher Kvs than the equivalent conventional two port control valve due to the integral differential pressure controller which maintains a constant low pressure drop across the motorised control element. However, small flow paths for good control of ultra-low design flows are unavoidable.
The DN10, DN15 and DN20 Frese Optima Compact PICV can pass a 2.5mm diameter particle down to 0.028 l/s flow settings and is relatively resilient to plugging from debris.
However, whilst the PICV can retain a full 2.5mm modulating stroke down to 0.008 l/s design flow, the flow path is reduced at these ultra-low flows and Frese recommend that system strainers are fitted in the terminal branch pipework, perhaps as part of the flushing bypass valve assembly at these low design flow rates.
Should a particle be trapped on the PICV outlet during back flushing then internal pressure across the diaphragm will increases resulting in the opening of the outlet to maintain a constant differential pressure across the valve inlet.
This self-cleaning action may allow the particle to pass though the valve but, should the particle be retained on the outlet seat, this will not affect flow through the valve.
Should a particle be trapped on the valve inlet during forward flushing or operation then this will reduce the Kv of the valve and actual flow rate achieved will be reduced, making it difficult to obtain repeatable flow during the commissioning phase.
BSRIA amended the BG 29 Pre-commission Cleaning of Pipework Systems publication in 2012 to include a flow side drain between the control valve and the terminal unit to allow the coil to be flushed directly at full flow without the flow passing through the two port control valve. Frese support this recommendation and offer flow and return side drains as standard on the Modula Direct valve assembly, which typically includes an Optima Compact PICV (shown in the picture above).
As the drive for improved system efficiencies and low heating return temperatures continues, ultra-low design flow rates will become more common.
![]() |
A valve assembly, including PICVs, from Frese |
However, other countries such as Denmark, have discovered that indirect control of terminal units can achieve high Delta T’s without the use of ultra-low flow rates that come with the associated, flushing, commissioning and control issues.
Figure 2 shows a pressure independent variable temperature injection circuit which promotes higher flow rates through the terminal units whilst the PICV throttles flow in the normal way to ensure secondary pumps can reduce speed at low load.
We think this design has many benefits in addition to avoiding ultra-low flows.
In particular, higher flow through terminal unit coils will ensure better heat transfer, improve system efficiency and climate control whilst ensuring the whole cleaning, flushing and commissioning process is more resilient to the impact of dirty system water.
Stephen Hart is managing director of Frese.