The modular solution
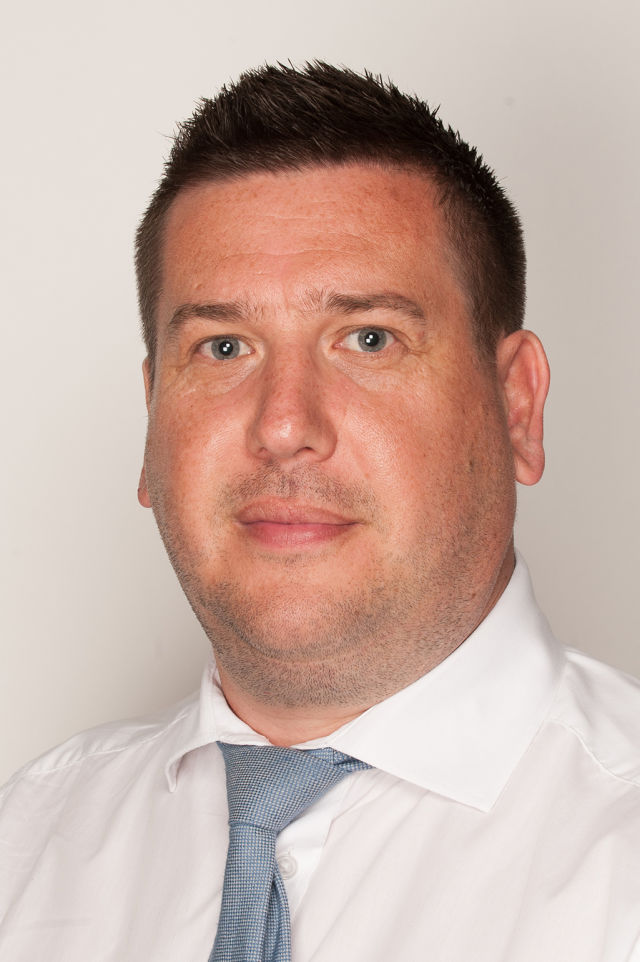
Graham Temple explains why modular chillers are proving popular for clients looking for a flexible and efficient approach to cooling.
There are a number of challenges facing building owners and managers today. Not least of these is that they must tackle ongoing requirements to reduce energy used in their buildings. This may simply be a response to the rising cost of electricity, but there are a number of areas of legislation placing pressure on those responsible for business energy use.
These include Minimum Energy Efficiency Standards (MEES), which require a minimum EPC rating (Energy Performance Certificate) for many commercial buildings. There is also a raft of new legislation relating to carbon emissions, including taxation aimed at driving down emissions from UK businesses – which include emissions from all energy used across the enterprise.
As well as energy efficiency, facilities teams will also be raising awareness of the F Gas directive, which has banned use (or re-use) of certain types of refrigerant which had commonly been used in air conditioning systems. The switch to low Global Warming Potential (GWP) refrigerants is a legal requirement, with penalties for non-compliance. There are also now growing issues with the rising cost of what were once common refrigerants – putting more focus on the ongoing costs of maintaining older air conditioning equipment.
HVAC systems, as big energy users and as users of refrigerants, are therefore under close scrutiny as businesses consider how to deal with all of these issues as efficiently and effectively as possible. Updating older air conditioning systems addresses several issues at once: an opportunity shift to low-GWP refrigerants which are more readily accessible; improved energy efficiency; and lower emissions.
There are other benefits too from an upgrade or refurbishment of the HVAC equipment in an existing building. New equipment delivers better and more reliable performance, reducing expensive maintenance call-outs and ensuring that occupants are more comfortable. Modern systems also come with an array of additional features such as advanced controls, which make them easier to operate in an efficient way.
The term ‘modular’ is increasingly heard in the field of building services. It is no longer necessary to specify and install large pieces of equipment in a single project. Modular kit provides a more modern approach, and benefits which are invaluable on both refurbishment and new-build projects. What’s more, modular equipment is provided to site in a highly ‘finished’ condition, requiring minimal installation effort, saving time and costs – as well as reducing possible installation problems.
The modular approach has in fact been in use in the UK for many years, in the form of the popular VRF systems. Their popularity is due in part to the fact that VRF systems offer improved energy performance based on use of variable speed fans and compressors.
Typically, they also require no installed redundancy so there is a saving on the capital cost. What’s more, VRF systems also offer limited impact in the event of a module failure. If one unit breaks down, it affects only a small part of the occupied space, not the whole building.
VRF systems have become mass-produced, commodity goods. Because of this approach to manufacturing the supply chain of components is robust and offers increased reliability due to modern manufacturing methods. Mass production accompanied with comprehensive quality control procedures ensures a consistent and better build quality. A reliable product and strong supply chain result in minimal downtime in the case of failure - a benefit for installers as well as their customers.
Modular chillers offer exactly this type of approach. Instead of a large, single chiller, a number of smaller modules are connected together to provide the end-user with the same level of output as the large, single chiller along with all the benefits of a mass produced commodity finished goods
The modular chiller has proved extremely popular in the Japanese market, where we find some of the most densely-populated cities in the world. It’s from here that we can learn lessons about HVAC approaches in UK towns and cities, where buildings are being constructed in constricted spaces, or where owners are looking to upgrade their HVAC systems.
Some of the key characteristics of modular chillers show why this is such a popular approach for designers, installers and end-users as an alternative to the conventional chiller plant. Modular chillers are pre-packaged, pre-piped and pre-wired modules which are tested in the factory before they are shipped to the site where only the water and power connections have to be made. Not only does this make installation errors less likely, it also reduces time on site for installers, and costs for end-users.
Another important consideration is that these small, light modules can be lifted to rooftops far more easily and in less space than the large chillers which usually require very large cranes, street closures and increased installation costs as a result.
What’s more, modular chillers offer greater stock availability and delivery times. As they are mass produced, modular chillers are part of the manufacturer’s ‘standard’ offering, resulting in a ‘just in time’ approach to ordering and delivery. Quick access to the product is very useful for projects with shorter construction durations such as universities, schools and sports arenas where downtime is minimal. Not only is this a time-saver at the point of installation, it also means that parts for repairs are also easy and quick to obtain.
Two of the most useful characteristics of modular chillers are their flexibility and scalability. The modules can be placed in a number of positions to accommodate almost any available exterior or roof space. Typical modular chiller design will save 35% space savings compared to a conventional chiller. Modular units can also be positioned at 90° to each other to fit conveniently into corner spaces. For designers looking to optimise ever-tighter roof and plant space, this is an enormous benefit over the large single-block chiller.
Scalability is particularly important for today’s buildings, where users and requirements for the HVAC plant are constantly changing. Modular chillers can easily be scaled up to meet new requirements.
Any new-build or refurbishment project will require a careful consideration of cost. One point which cannot be overlooked is that the capital costs of modular chillers tend to be higher than those of conventional chillers. However, there are a number of cost savings relating to the modular approach which must be borne in mind by specifiers and clients.
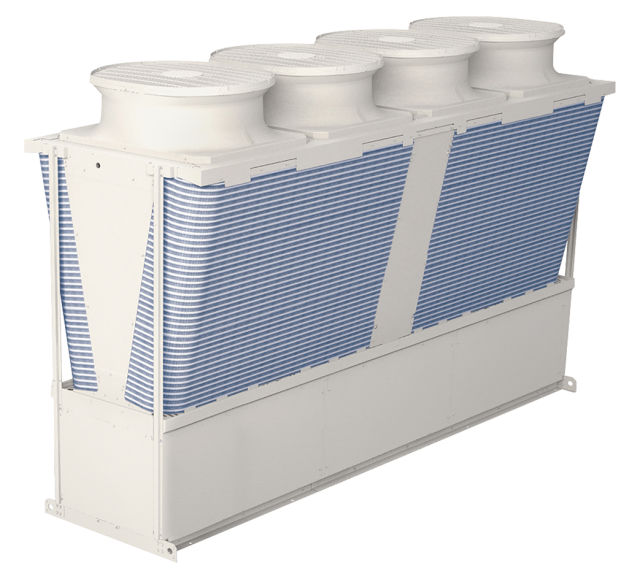
One of the most significant is in lower lifetime energy use costs. The modular approach to chillers allows designers to meet the requirements of a project far more closely than with a traditional chiller. Modular chillers offer significantly better seasonal part-load efficiencies, which mean that it uses less energy, and costs less to operate, in the long-term.
Modular chiller technology is advancing all the time, and the market is seeing more sophisticated approaches to controlling chillers – creating more opportunities for energy saving. One of the latest examples of this is the Mitsubishi Electric eSeries chiller which offers built-in controls that are designed to integrate easily into a building management system (BMS).
Rather than seeing each module as a separate item on the BMS the controls systems ‘sees’ the modules as a single unit. This greatly reduces integration time for the controls engineer and cuts down on the likelihood of errors. What’s more, while the BMS sees a single point for ‘writing’ instructions, it ‘reads’ all the modules individually. This means that if a single compressor fails or operates outside of normal parameters, the BMS can send the maintenance team an alarm. A further saving from this level of BMS integration is that there is no need for the additional cost of chiller sequencers to ensure effective operation of the modular chillers.
Another cost saving is that modular chillers do not require the same like-for-like redundancy in chiller plant design that is found in the conventional chiller plant. Multiple compressor circuits mean that redundancy is built in. For example, in an installation of 6 modular chillers of 180kW each, if one compressor breaks down, the system can still function with 8% capacity loss. If the compressor in a large single chiller ceases to work, the system loses 50% capacity.
Finally, when considering the costs of a modular chiller project, the scalability factor is also important. Modules can be added in a staged approach, allowing clients to achieve their HVAC upgrade over time. Given the increasing flexibility required of today’s buildings, it is also a benefit for clients who want to take a longer-term approach to planning their future building services.
As our urban environments become increasingly mixed, with hotels and offices abutting modern urban housing, the noise factor is one that local authorities are keen to control.
Modular chillers are by their nature much quieter than conventional chillers. The variable speed inverter fans which make modular chillers so energy efficient also mean that these products operate with much lower sound levels. For example, a conventional large capacity chiller operates at over 100db ; the Mitsubishi Electric eSeries modular chiller runs at 77db. Even if there are 20 units on a rooftop, this would still produce a lower sound level than the conventional chiller (see Table 1)
This is also another cost-saving to bear in mind – sound attenuation, if required can cost up to 25% of the cost of a conventional chiller.
Table 1: Selection Analysis
Capacity requirement - 1 mW
Selection | Redundancy | Footprint | Noise per chiller/module | |
Sound Pressure Level dB(A) |
Sound Power Level dB(A) |
|||
Low noise Inverter Screw | 2 X 66% SFF | 102.55 m2 | 72 | 94 |
Low noise Inverter Screw | 3 X 50% SFF | 140.68 m2 | 72 | 93 |
13 X 90kW modules | n + 1 modular | 58.22 m2 | 65 | 77 |
7 X 180 kW modules | n + 1 modular | 24.82 m2 | 68 | 86 |
Modular chillers are part of a growing trend in building services. The modular chiller approach works for designers because they can more closely match the specified equipment to the requirements of a project. By minimising redundancy requirements, equipment is less likely to be over-sized – making it more efficient from the start.
For installers, modular chillers are products which are easy to source, and designed for smooth installation. Quality of manufacture means that warranties are longer, offering peace of mind to those working on site. And for those involved in ongoing maintenance services, spare parts are easily available.
For end users, today’s modular chiller is the modern solution for HVAC needs. A quiet, efficient and flexible product that can grow with their building requirements. There can be no doubt that we will see a growing number of projects adopting this technology for better outcomes for all involved.
Graham Temple is marketing manager for Mitsubishi Electric UK