Making modular mainstream

The modular building market is an alternative to traditional methods of construction. How can we all benefit from its expansion?
Coronavirus has had a dramatic effect on the way we live, work, and socialise in a short space of time. Unfortunately, this doesn’t show any material sign of returning to normal any time soon. In light of the pandemic and the social distancing restrictions that have been brought into place across the UK, one area that does stand to benefit from this is the rise of the modular building market. The buildings we live, work, and play in account for over 40% of the nation’s energy consumption and carbon emissions. If the UK is to realistically reach its ambitious carbon reduction targets, the traditional methods of construction need a significant overhaul.
A key ingredient for a green recovery
Before the pandemic hit, the global modular build market was set to be worth over £165bn by the middle of the next decade. Now with office spaces, schools, accommodation and even healthcare facilities looking to return to some kind of normality, while doubling or tripling its existing space requirements, the modular building market is poised to really take off. This is primarily because it offers easy, cost-effective, more environmentally friendly and more rapid expansion to meet the needs of a market impacted by social distancing.
Support for the long-running Climate challenge
It’s not just the pandemic that is acting as a driver for the growth in the modular buildings space. As citizens become more climate conscious and we are being exposed to greater awareness of our carbon footprint on a near daily basis, traditional construction has already been coming under the spotlight. Cement alone is a source of about 8% of the world’s CO2 emissions, accounting for nearly 6% of the UK’s greenhouse gas emissions. Cement has such a large carbon footprint, if it were a country, it would be the third largest emissions producer, behind China and the US.
In comparison, the modular building market is much more efficient. Modular buildings are constructed offsite which means they can reduce 90% of the waste generated from traditional construction methods, while using 67% less energy to produce a modular building. Modular buildings are also built to the higher sustainability standards such as BREEAM, or PassivHaus.
A rapid solution
The virtue of being built off-site and then assembled when ready means that construction time is significantly reduced, often by as much as 50%. Multi-site works can be developed simultaneously, allowing for more projects to be completed in half the time, and occupants in sooner. This means that everything from the heating, cooling and ventilation systems, to the lighting requirements and the windows can all be installed in modules off-site, ready to be fitted together once required. It can all be done to deliver a more energy efficient building as well.
This means that modular buildings can be readily equipped with the most advanced technologies to deliver modern levels of comfort and well-being to occupants. What’s needed are heating, cooling and ventilation systems that become a seamless part of the solution, with innovative HVAC products that are the ideal fit for modular building, construction and management throughout their working life. Using products such as modern air conditioning, heat recovery ventilation and renewable heating helps ensure efficiency, reliability and quality are at the forefront of the manufacturing process to match the improvement in the construction standards that modular buildings can offer the industry. Whether that is air conditioning with the latest, lower global warming potential refrigerants (R32), renewable heating through modern air source heat pumps such as the advanced Ecodan range, or heat recovery ventilation units such as the Lossnay system to deliver energy efficient fresh air.
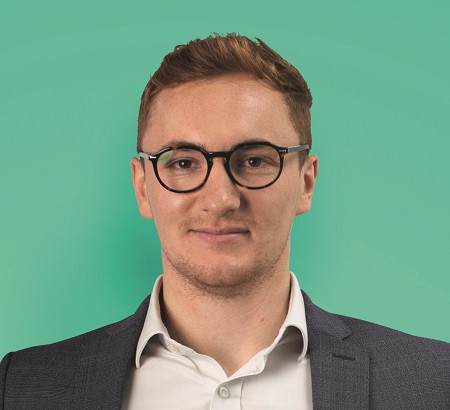
A high quality, long-term solution
Modular buildings can address a lot of concerns in the current environment and offer a viable, sustainable long-term future for UK construction, especially as it struggles to return to pre-COVID-19 levels of activity.
Modular buildings adhere to the same building regulations and standards as traditionally constructed buildings. This means adhering to building regulations such as thermal performance (U Value), fire safety, sustainability and acoustics. Being built off-site means the modular panels are constructed in a covered, controlled environment which brings precision and quality control.
A job for the future
Construction jobs come with all sorts of caveats and restrictions, physically for those that work on site, but also because of the UK’s weather. Inclement weather shuts down construction for days at a time, a factor that’s only going to increase as the impacts of climate change are felt. With modular buildings however, these can be built inside a factory space and then assembled on site. Working at ground level also brings the added benefits of diversifying the workforce with a more easily accessible environment opening up opportunities for people of all abilities.
By creating regional hubs, local jobs can be created in the development of local construction projects. Universities and colleges can offer courses in new building developments and modular construction practices that help to train a new generation of apprentices and builders.
Conclusion
The way the world works has changed dramatically over the last few months. While there has been a lot of change, one thing is for certain, things won’t go back to the way they were for the foreseeable future. With the UK population pushing for a green focused economic recovery from the pandemic, modular buildings go a long way to helping achieve that reality. Everyone involved in the built environment has to work together to understand that traditional ways of construction – in isolation - are no longer the sole viable routes for a 21st century sustainable outlook and a clean-tech, digital focused approach to construction is required. Modular is also well positioned to quickly and conveniently create the space that many industries require to adhere to social distancing. As well as creating green jobs in the construction sector, it also helps to go some way in reducing that 6% of cement pollution from the UK’s annual quota. The strengths are clear to see. Isn’t it time to start making modular mainstream?
Dan Smith is Corporate Business Development Executive at Mitsubishi Electric